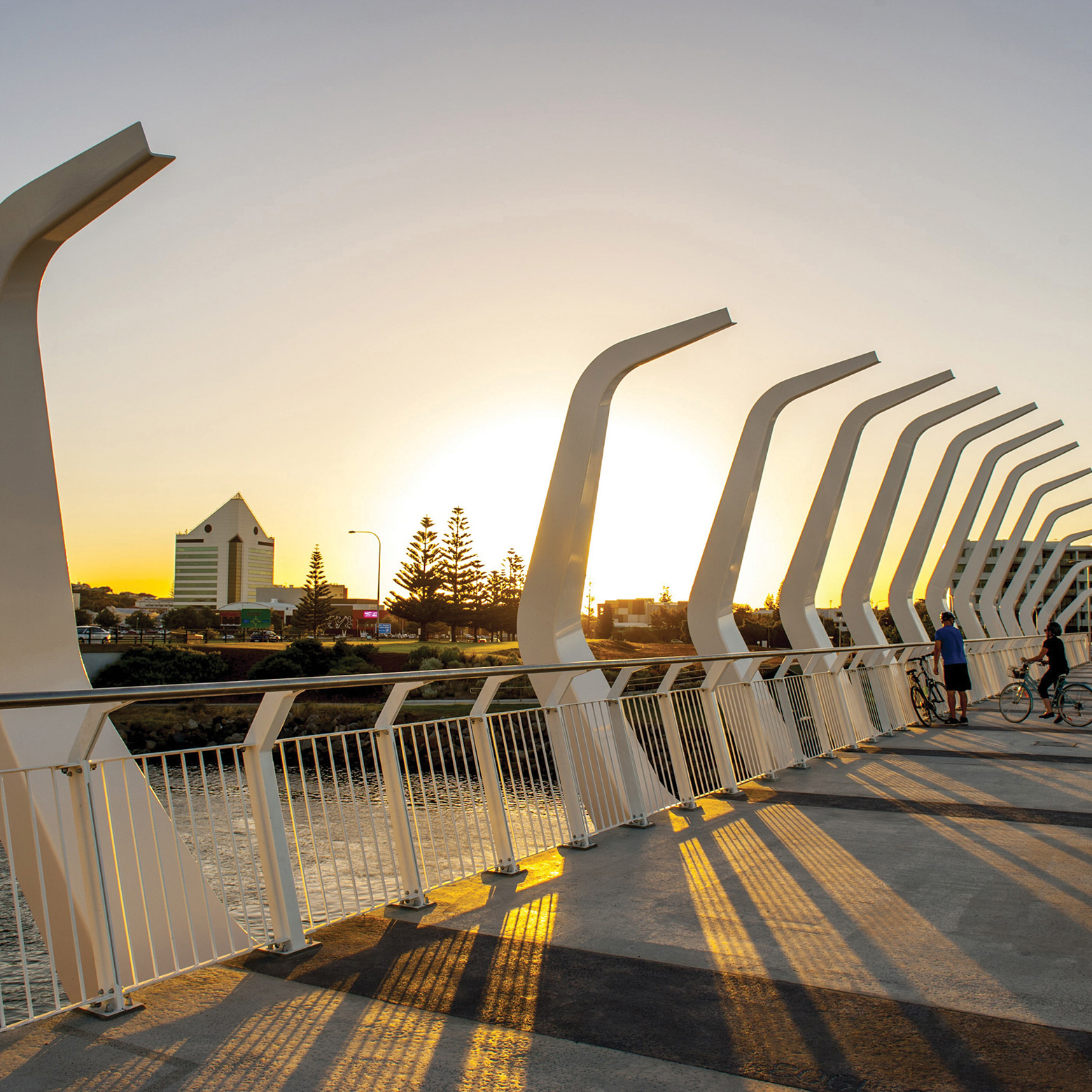
Christopher Cassaniti Bridge
In the Christopher Cassaniti Bridge, engineering and architecture come together to produce a striking double-helix structure fabricated from XLERPLATE® steel (250 grade).
Words: Leanne Amodeo.
Photography: Landcom
Project Summary
The Christopher Cassaniti Bridge is Australia’s first double-helix bridge and provides the connection between the residential Lachlan Line’s development to North Ryde Metro Station, spanning the M2 Motorway and Delhi Road without interruption to traffic.
In the Christopher Cassaniti Bridge, engineering and architecture come together to produce a striking double-helix structure fabricated from XLERPLATE® steel (250 grade).
Sky Line
The diversity of pedestrian bridges across Australia reveals an infrastructural typology where design innovation reigns. Engineering considerations are always foremost to ensure safety and accessibility, but there’s so much scope for aesthetics. It’s little wonder the end result often divides public opinion and gets people talking.
From the sweeping curve of the Adelaide Riverbank Pedestrian Bridge to the colourful explosion that is the Koolangka Bridge (The Kids’ Bridge) in Perth, there’s no shortage of new statement-making pedestrian bridges enlivening the urban landscape.
Add to this list the recently completed Christopher Cassaniti Bridge in Sydney’s Macquarie Park and expectations for what can be achieved design-wise have been elevated. Initially known as the Lachlan Line Bridge, the 170-metre structure was formally renamed to honour a young apprentice formworker who died on a nearby unrelated construction site. The Christopher Cassaniti Bridge is Australia’s first double-helix bridge and provides the connection between the residential Lachlan Line’s development to North Ryde Metro Station, spanning the M2 Motorway and Delhi Road without interruption to traffic. The project involved a close collaboration between engineer Arup, architect KI Studio, contractor Arenco Daracon Joint Venture (ADJV) and fabricator S&L Steel.
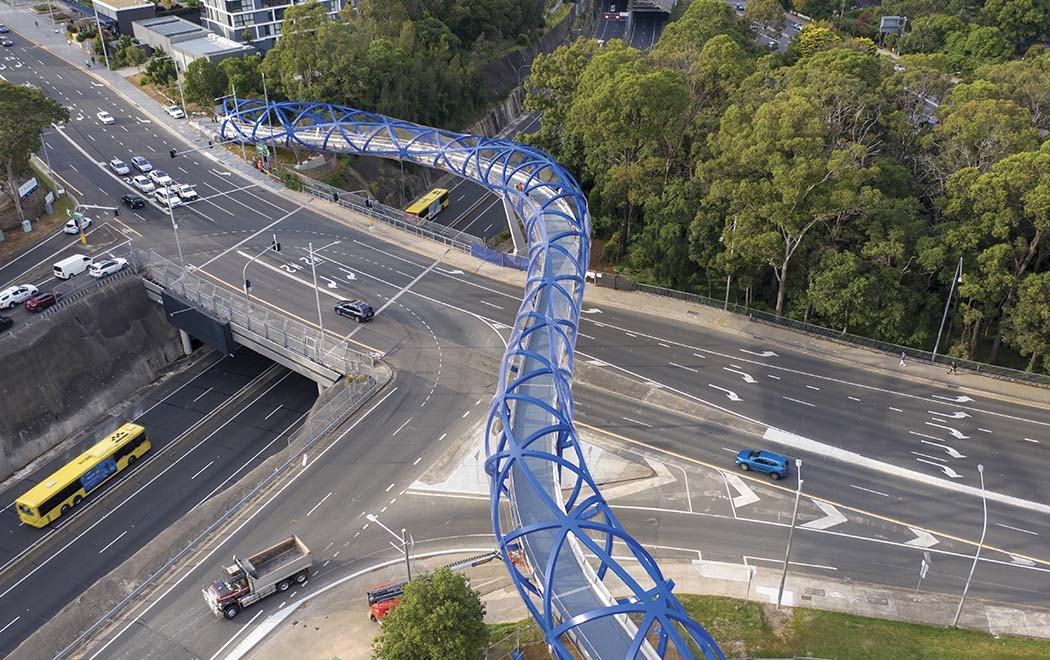
In regards to the aim of client Landcom (the New South Wales Government’s land and property development agency), their brief was straightforward. As developer of the ambitious Lachlan Line urban regeneration project, which includes a proposed 2,700 new homes for 5,000 residents, they needed an efficient piece of infrastructure that would allow pedestrians and cyclists safe access across to the train station. However, the brief’s simplicity belied the bridge’s extreme complexity. Not only did it have to span two roads, there was also limited available space for the entry points and piers.
The bridge’s overall geometry was initially driven by an engineering assessment that involved a parametric study to find the shortest possible bridge length. So the ensuing design was conceived and led by Arup, in conjunction with KI Studio.
As Arup structural engineer, Xavier Nuttall, explains: “We wrote our own computer code that found the alignment of the bridge, and once we set that alignment we could work out the minimum feasible length and pier locations, given the surrounding topography, the levels of the land and how high the bridge needed to be,” Nuttall says. Indeed, Arup captured the design process in an entirely digital workflow connected by computational code, which allowed for greater efficiency. When something in the design changed, for example, the software would automatically update all other aspects of the design accordingly.
With the line on the map drawn, so to speak, the engineers then had to determine what the right type of structure would be to support this type of bridge. “And that’s when the idea of an enlarged tube-like or tubular structure came into play,” says Nuttal.
“Because of the alignment’s curves, there’s a lot of tension in it and a tubular-type structure is very good at resisting tension.” The resulting double-helix form is not purely about aesthetics, then, although its sinuous curves, which are finished in an electric blue paint colour, do eloquently snake across Delhi Road and the M2 Motorway to dramatically striking effect. Rather, the helix structure is a response to the types of forces at play in the bridge’s alignment.
With regards to its construction material, the only viable option was mild (low carbon)1 steel, in this case, BlueScope XLERPLATE® steel (250 grade). Put simply, the design could not have been achieved using any other material because the bridge needed to reach spans of up to 72 metres between piers and this requires a very light material, as anything heavier could not be accommodated. Steel is easily manipulated from a fabrication perspective, too, and this was important to achieve the different necessary-forced capacities.
1. The terms ‘low carbon’ and ‘medium carbon’ steel refer to the carbon content of the metal alloy and not to the carbon dioxide (CO2) emissions associated with the product.
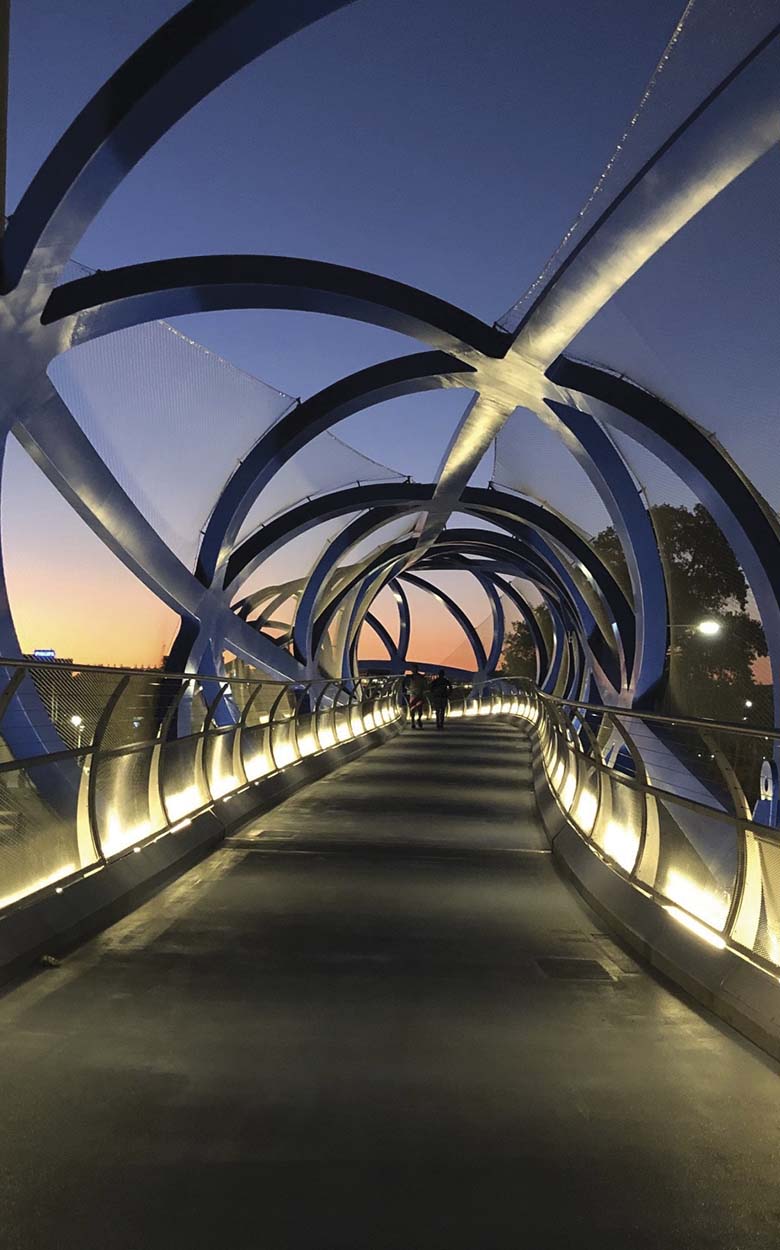
“We really did want to create a sculpture in the landscape... And the bridge itself combines form, texture, colour and motion, making the end users’ journey all the more engaging and unique”
Miguel Wustemann Director, KI Studio
Hollow box sections were used, instead of the traditional circular section, in order to enable each side of the section to be optimised with different plate thickness in response to structural demand. “If you can imagine a typical concrete beam has the same shape all the way along the span. Well, that’s not the case here,” says Nuttall.
“The XLERPLATE® steel (250 grade) mild steel plate thickness could be adjusted at any point on the bridge to make full use of the material’s properties and that was the main reason we used it,” he says. This makes for a sustainable outcome because no steel plate is any thicker than it needs to be – the box sections range in thickness from 8mm to 32mm – thus eradicating excess consumption, minimising steel tonnage and reducing embodied energy of the structure.
Arup also required a construction material they knew would perform well. The engineers had very strict deflection criteria in terms of how they defined the geometry of the bridge through an understanding of how much it would sag under its own weight. Bridges that are 70 metres long (some 100 metres shorter than the Christopher Cassaniti Bridge) can move anywhere up to 200mm due just to their own weight. It was therefore paramount the engineers were confident in the way the material behaved, so that the 5.5-metre vehicle clearance envelope would not be encroached upon. A tight 50mm tolerance was built into the design and the steel has behaved exactly as they predicted, achieving the necessary clearance to the road.
Over 3,600 steel plates were used to form the 335-tonne double-helix and each one is unique. They were initially laser-cut, then rolled into a particular shape and finally welded together to create the twisted, curved box sections. This resulted in 260 beams of different shapes and thicknesses that were in turn welded together at the connections to create the double-helix. It was a challenging undertaking successfully accomplished by S&L Steel, who fabricated the structure in their workshop at Glendenning, approximately 50 kilometres west of the bridge’s site. S&L Steel also assembled the helixes off-site, before dismantling and transporting to site in four separate spans. This was no mean feat, and Arup developed and designed transportation, and lifting assemblies for each segment so as to not overstress the permanent elements. One of the spans was 70 metres long and weighed 130 tonnes. It was lifted in one piece using a 500-tonne crawler-crane from Delhi Road, which had to be closed for the lifting.
The installed double-helix measures 7.8 metres in diameter at its widest and 5.5 metres at its smallest. It comprises the bulk of the bridge structure in its entirety and so the rest of the material palette is relatively pared back. Stainless steel was used for the deck in a decision driven entirely by practical requirements.
“Stainless steel doesn’t need regular maintenance and so we used it in areas that are difficult to access and inspect,” says Nuttall. “Of course, anywhere that needs regular access has been constructed from BlueScope mild steel.” The piers and foundations are concrete, as are pavers which punctuate sections of footpath at the bridge’s entry points.
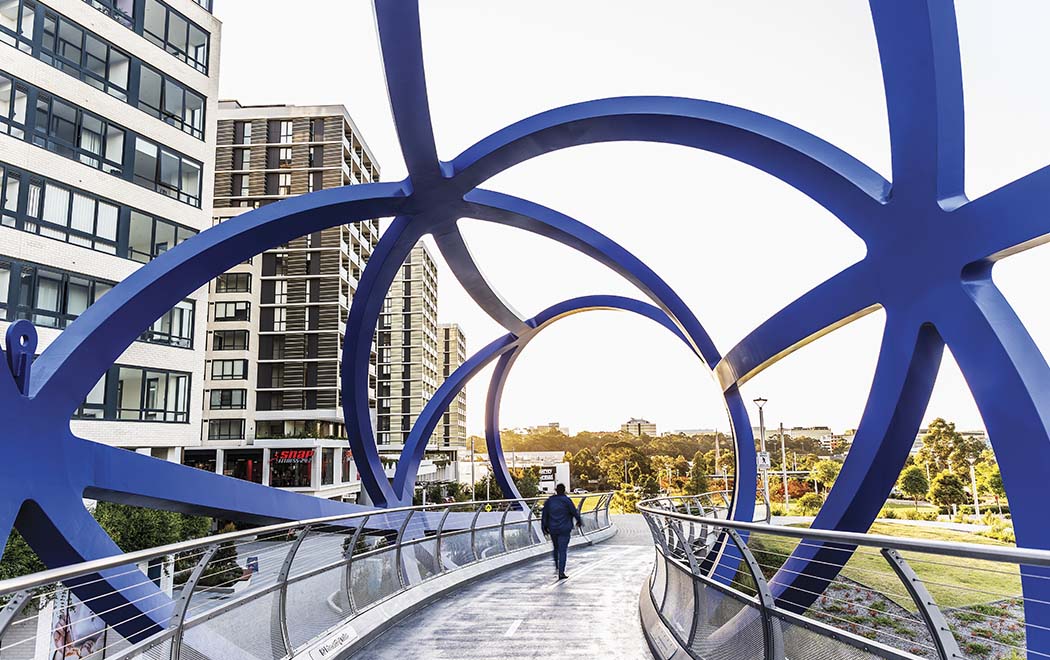
Much consideration was given to the Christopher Cassaniti Bridge’s surrounds and both the engineers and architects were mindful to emphasise a connection with the natural environment, specifically a reserve south-west of the structure.
The bridge very much unfolds into its entry points where thoughtfully configured landscaping prioritises accessibility. These schemes are light, bright and thoroughly modern and also serve to embed the bridge in its broader context.
As architect and city and regional planner and KI Studio director, Miguel Wustemann, explains, “We really did want to create a sculpture in the landscape. The helix’s fluid form gives the structure a sculptural quality both from within and from the outside. And the bridge itself combines form, texture, colour and ‘motion’, making the end-users’ journey all the more engaging and unique, while delivering a memorable landmark.”
This sense of connectivity is implicit when walking or cycling on the bridge, too. At no point is there a dark spot and at all times there’s good visibility. While this was driven by a safety requirement that ensures clear sight-lines for cyclists, it also maximises the bridge’s experiential qualities. Pedestrians can feel secure making the journey from one side to the other and, because of the structure’s openness, they have a visual connection to the sky, which helps to keep their eyes off the road below.
The helix structure’s electric blue finish also works to reiterate this sky connection, however Nuttall admits the colour choice was not intentional from the very beginning. “I’d chosen the colour blue in our digital model as a way of differentiating it from all the other elements,” he says. “The columns were pink and so it wasn’t about reflecting the structure’s actual colour. But the architects thought it worked really well and when we presented a few colour schemes to the client, everyone agreed on the blue.” The lighter colour means the bridge doesn’t heat up too much, whereas a darker colour would have made it get very hot, causing the bridge to expand and contract a lot more.
Thorough peer and independent reviews by different engineering companies and contractors ensured the structure’s design was correct from every conceivable angle. This guaranteed a smooth construction process with no unforeseen dramas and when it came to the official opening, the local community couldn’t wait to see it.
Nuttall was in attendance and recalls the overwhelmingly positive feedback. “I remember one of the first people to cross the bridge had been watching it being constructed for a year and they were so excited to walk across it,” he says. “Since then, it’s also received industry recognition with multiple national and international awards.” It’s a hugely successful piece of infrastructure that will stand the test of time, bolstered as it is by a robust BlueScope steel structure that’s as aesthetically pleasing as it is high-performing.
STEEL DETAILS
A TECHNICAL DIVE INTO THE CHRISTOPHER CASSANITI BRIDGE
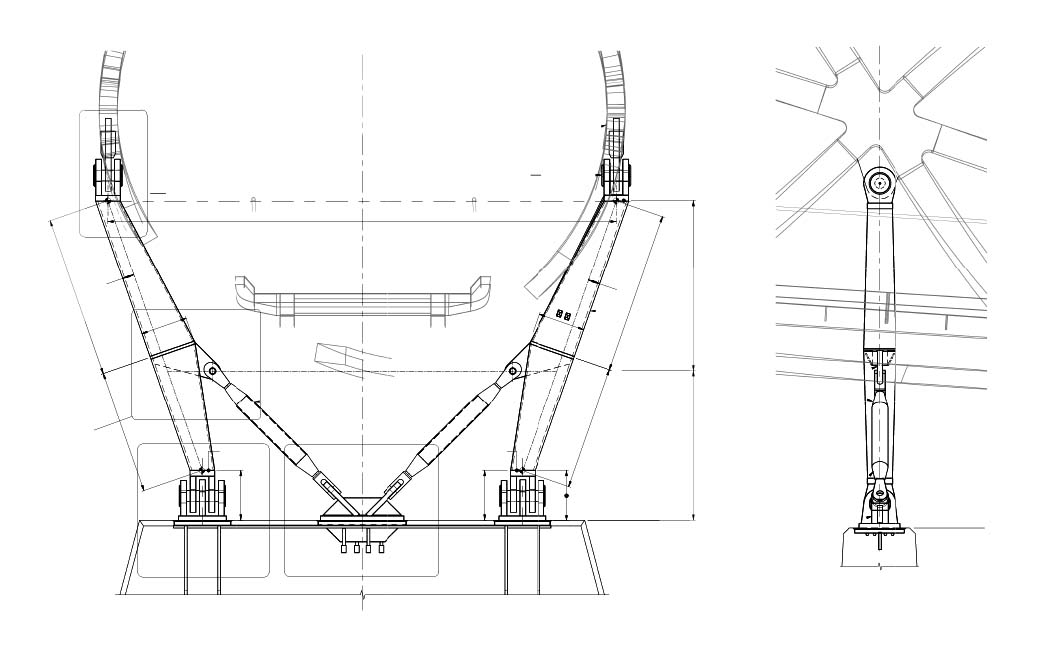
The Christopher Cassaniti Bridge is one of Arup’s first projects to use an entirely digital workflow, so the engineers didn’t produce drawings. Rather, everything was communicated in a 3D model. While this digital approach initially allowed the engineers to determine the shortest alignment for the bridge, it also let them innovate during the design process, with changes updating in a matter of minutes instead of weeks.
As Arup’s Xavier Nuttall explains: “We could change the shape of the helix and the orientation of the diagonals within it to best suit the demands of the structure.
So where we would see higher forces within the structure, which is near the piers, we could use our digital tools to make it bigger and then shrink it where the forces were lower. It meant we could use less steel for a more sustainable outcome.
Overall, this digital workflow produced greater efficiency, as it created architectural surfaces, defined the set-out and centreline geometry for analysis and fabrication, and built and analysed a series of models, amongst other functions.
It also updated Revit documentation and saved BIM models that contained all the BlueScope mild steel data.
When it came to the bridge’s verification, a point-cloud-scan was used, which was then compared to Arup’s digital model. This involved generating a contour map depicting where the point-cloud indicated the structure was, and compared it to where Arup had predicted it should be.
Each of the points were colour-coded, making it easy to identify in real-time if the structure’s positioning was accurate.
It was also necessary to produce a 3D model of the over 3,600 steel plates in order to assist the fabricator, S&L Steel. So Arup developed a software that analysed 164 unique doubly-curved node surfaces and identified their individual best-fit equivalent cylinder.
This in turn generated the simple roll radiuses and roll directions, which allowed the fabricator to unroll the geometry and laser-cut the shapes from the BlueScope mild steel plate.
Arup’s digital approach to geometry, engineering and design sets a new benchmark for future infrastructure works across the country, especially pedestrian and cyclist bridges such as this close space.
It also highlights the positive confluence of engineering and architecture in giving rise to an impressive structure that owes as much to one skill set as it does the other for its intricate, striking form.
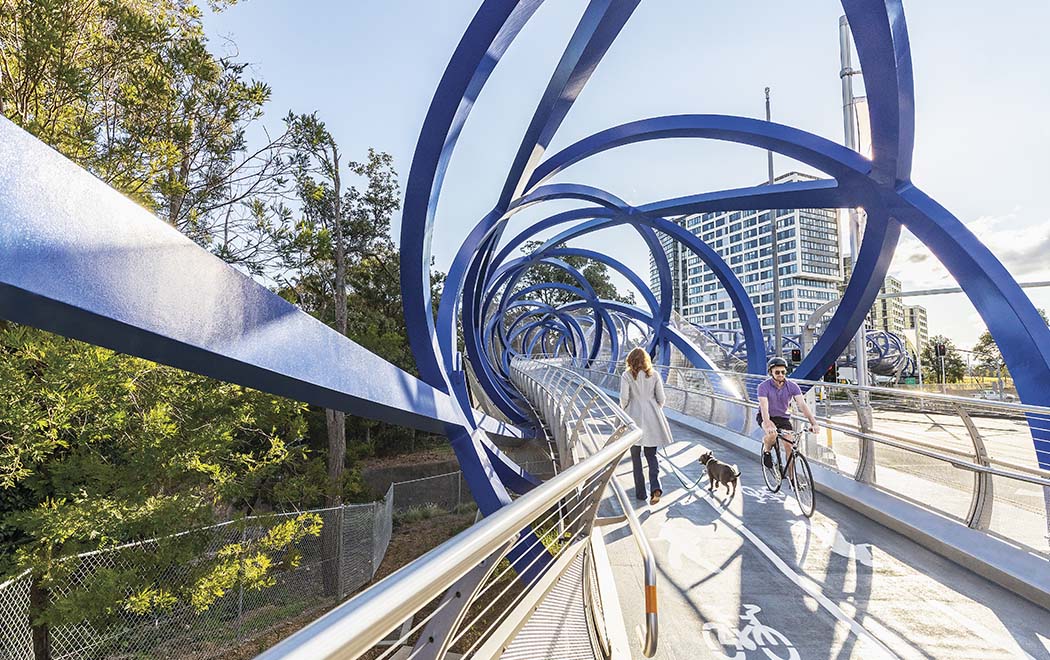
Project information
Architect
KI Studio
Project
Christopher Cassaniti Bridge, New South Wales
Awards
- 2020 ASI National Steel Excellence Awards – Engineering Projects
- 2020 ASI Steel Excellence Awards NSW Division – Engineering Projects
- 2020 Master Builders Association NSW Excellence in Construction Awards – Best Use of Steel
- 2020 Master Builders Australia National Excellence in Building & Construction Awards – National Civil Infrastructure Award over $25m
- 2020 Master Builders Association NSW Excellence in Construction Awards – Open Price Category
- 2020 Good Design Australia Good Design Awards – Architectural Urban
- 2020 Good Design Australia Good Design Awards – Engineering
Location
Macquarie Park, New South Wales View on Google Maps
Copyright® 2022 BlueScope Steel Limited ABN 16 000 011 058. All rights reserved.
No part of this publication may be copied, reproduced or distributed without consent. BlueScope Steel Limited, to the extent permissible at law, is not liable to any person for loss or damage arising from reliance upon information contained in this publication. The articles featured in STEEL PROFILE® are sourced, written, fact-checked and curated by Indesign Media Asia Pacific with editorial contribution from BlueScope Steel Limited. Any statements or opinions attributed to a person are the views of that person alone. The decision to use any particular product or material in the projects featured in this publication was made by the team involved in each project and not BlueScope Steel Limited. While care has been taken to verify the accuracy of details in this publication, BlueScope Steel Limited assumes no responsibility or liability for any errors or omissions in the content of this publication. All information is provided with no guarantee of completeness or accuracy.
Images shown throughout have been reproduced to represent actual product colours as accurately as possible. However, we recommend checking your chosen colour against an actual sample of the product before purchasing, as varying screens and devices may affect colour tones and finishes.
Every project is different and not all products are suitable for all applications, projects and environments. Some products may perform better than others in certain applications and conditions.
BlueScope recommends routine preventative maintenance for eaves and other "unwashed areas" of structures that may not be regularly cleaned by rainfall. To determine the most suitable material for your project, please contact your supplier or visit steelselect.com.au. For information about product maintenance, including preventative maintenance, please call BlueScope on 1800 753 658. To determine whether a warranty may be available for use of a product in your particular project, please visit bluescopesteel.com.au/warranties or call BlueScope on 1800 753 658.
XLERPLATE® is a registered trademark of BlueScope Steel Limited.
Submit your project
We encourage you to share your projects for consideration in a future issue of STEEL PROFILE® magazine. We invite you to submit projects that feature a ground-breaking or an innovative use of steel. We love celebrating and writing about such projects!