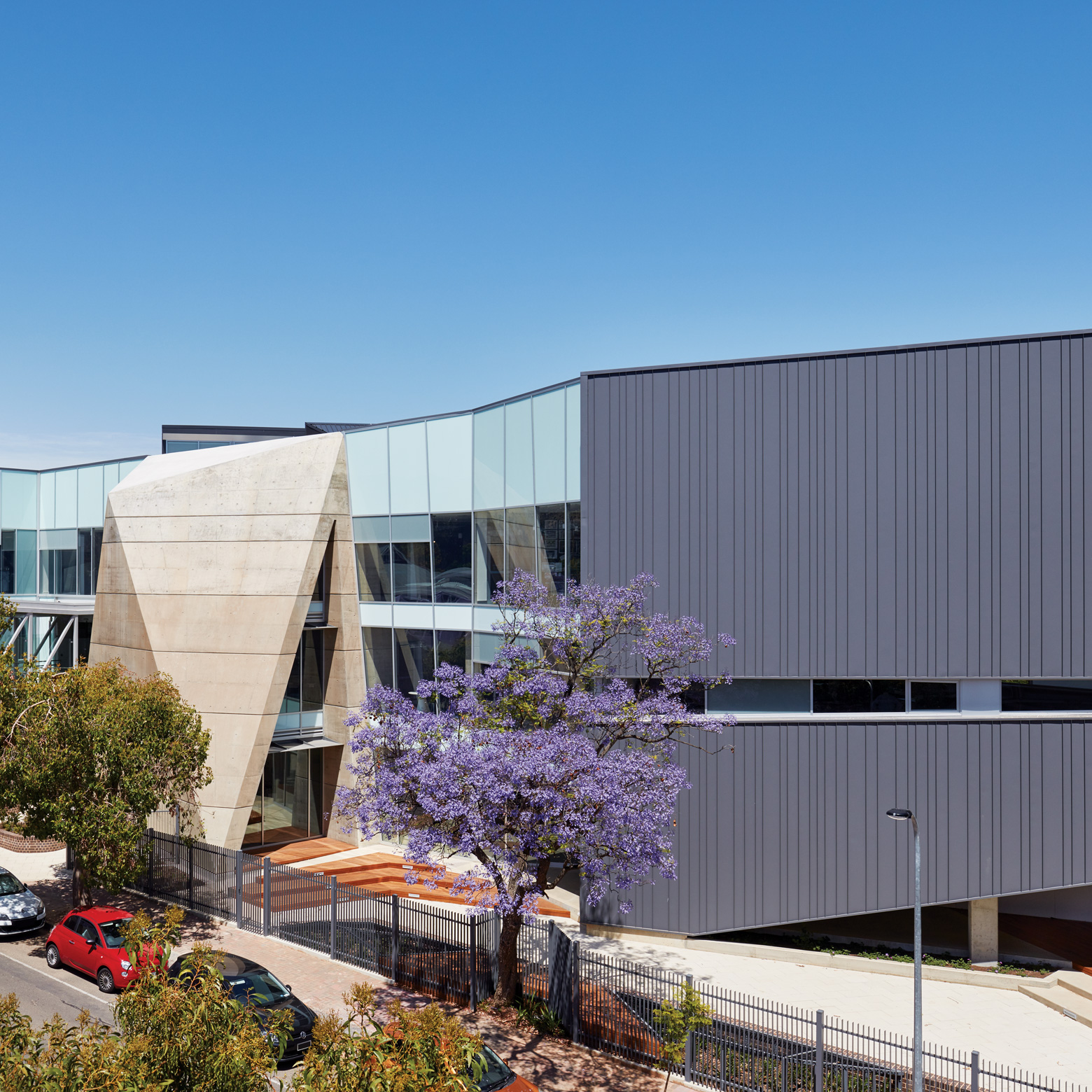
Arts West, University of Melbourne
There's an abundance of innovation to be found in this ground-breaking project where steel has been imaginatively used to unite a number of physical elements and conceptual ideas with striking effect.
Words: Micky Pinkerton.
Photography: John Gollings
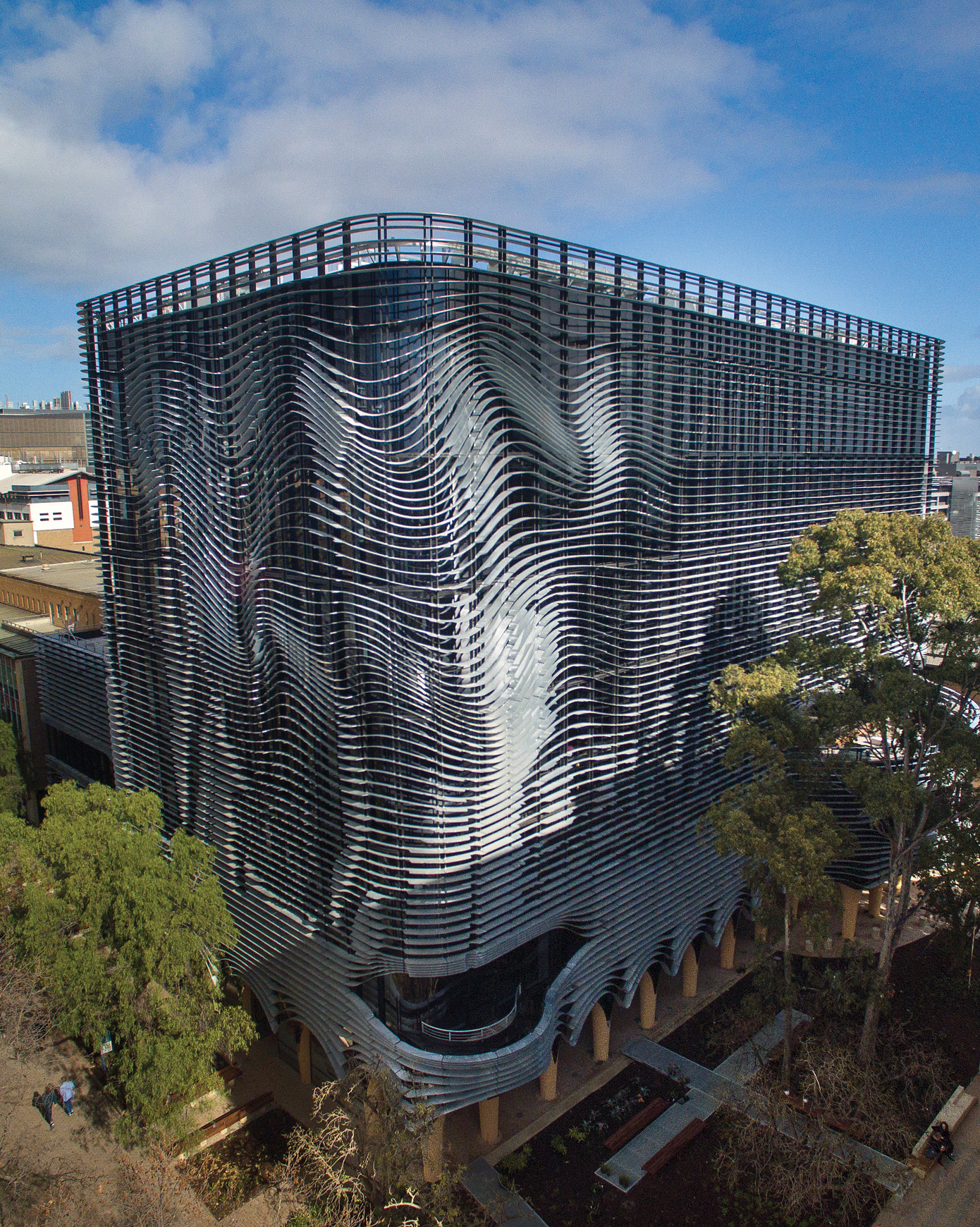
Project Summary
With the building’s signature steel fins: four-and-a-half thousand of them, all made from 8mm XLERPLATE® steel (250 grade) and the vast majority of them individually unique. Arts West, University of Victoria is truly one of a kind.
Collective Experience
This story about Arts West, the University of Melbourne's Faculty of Arts building, is a story about collections – we've got time for three, here. Let's start with the building's signature steel fins: four-and-a-half-thousand of them, in fact, all made from 8mm XLERPLATE® steel (250 grade) and the vast majority of them individually unique.
Each fin made from XLERPLATE® steel (250 grade) is a thing of beauty in its own right, from its shape and patina, to its strength and durability. Gather these fins together as a group and it’s an impressive amount of steel; arrange them in a curated way into the collection that you see here, and 4,500 fins transform into something else altogether. To say that these fins are greater than the sum of their parts is to reduce this achievement in materiality to cliché and gives no sense of the scale of the task. But let’s move on...
Next are the collections of objects. At the micro level, we have the University’s esteemed compendium of artefacts dating back three millennia: paintings, books, bronzes and ceramics representing the attitudes and identities of the past that are now being re-interpreted through contemporary curricula. Whereas at the macro level, this is a collection of buildings and built elements: an efficient, steel-beamed new commercial structure and two smaller existing buildings that have been consciously swathed in the sculptural facade generated by all those precisely arranged fins. These micro and macro collections of objects combine at a meta level to deliver no less than the audacity of architecture, where art meets science, and a building has become a physical representation of how ideas are forged into new learning.
And finally, there’s the collection of knowledge that made it possible. The University of Melbourne and its stakeholders wanting to recognise both a rich past and a changing world. ARM Architecture and Architectus, helping the University to translate that vision into the built environment, ensuring that education is integral to the teaching spaces, informal spaces and even the facade.
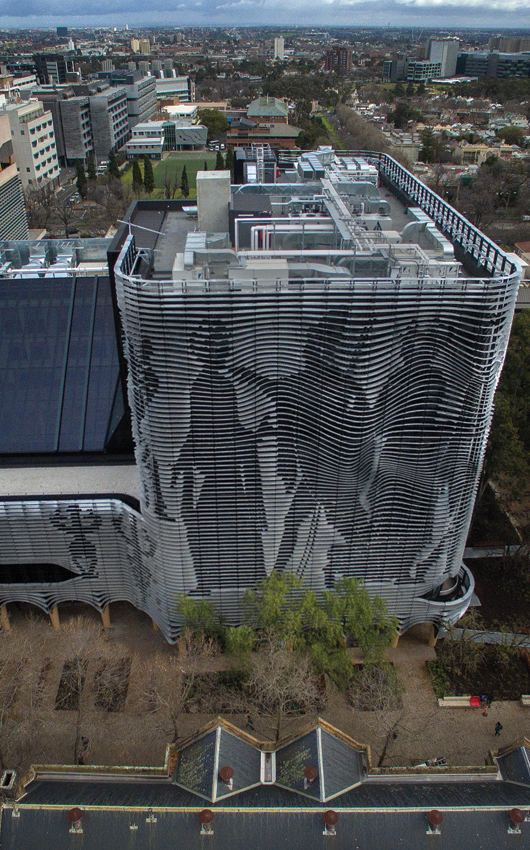
Also Kane, Inhabit and Fabmetal, amongst many others, combining years of experience in construction and skill in working with steel to push those ideas into reality working with [builder] Kane on the buildability side, to working with [steel fabricator] Fabmetal on modifying the detailing. It is almost unnecessary to mention that this project won the Australian Institute of Architects National COLORBOND® Award for Steel Architecture. Of course it did. That it has won a dozen more awards tells you that Arts West is a project of lasting significance.
Its facade solution occupies a vital point in ARM’s oeuvre: building on the conceptual ideas explored in the William Barak building, and then being a pilot for the steel innovation taken a few steps further in the more recent Monash Chancellery project.
These collections of materials, objects and knowledge interweave and overlap in Arts West, beginning with the decision to use a double facade. “The reason we do this is it means that the inner facade can do all the things it needs to do, thermally, and just from a vision point of view, it can be cost-effective, it doesn’t have to do a whole lot of decorative things so it can be absolutely commercial,” says ARM’s founding director, Ian McDougall.
“If you make a highly specialised facade, you get two or three tenders, so by making it an absolutely standard, high-performance exterior, lots of people can tender, and you therefore get a competitive inner skin and then the outer skin can do what it needs to do.”
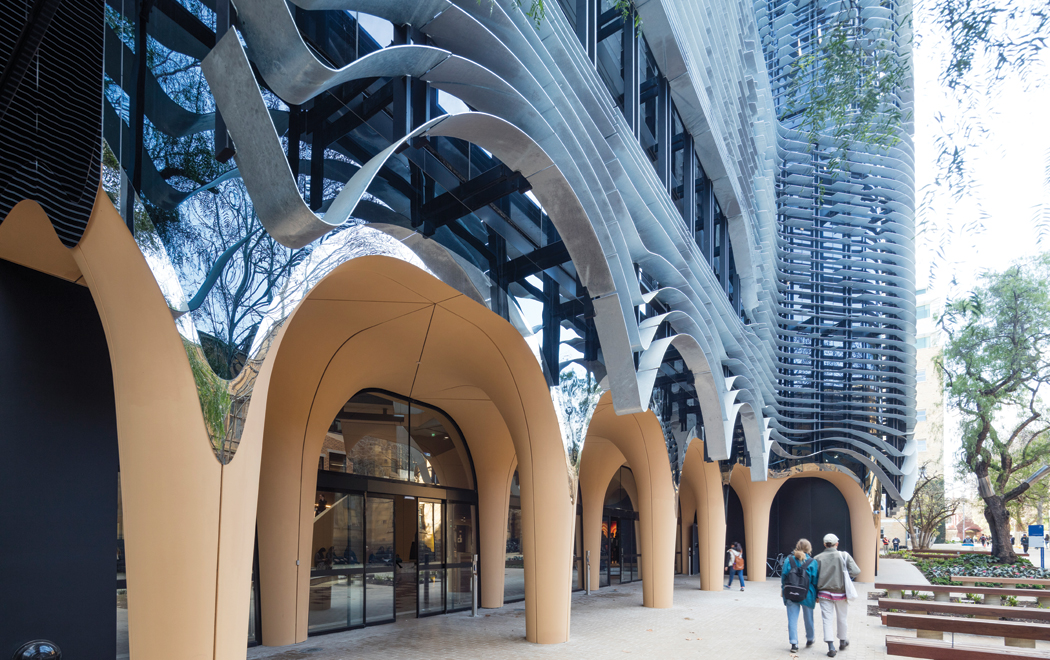
In this case, what that outer skin needed to do was function-shading for what is essentially a large glass building, via a form that reflected the substance and contribution of the scholarship that was occurring within the Faculty of the Arts. The representative figures and images from the Faculty’s collection that were chosen by the University for embossing on the facade in a giant scale included a 19th-century bronze sculpture, an ancient Greek vase and a painting by 19th-century Indigenous artist, Tommy McRae.
Steel was selected for the fins for various reasons.
“The fins, being steel, provided us with the opportunity of keeping them thin and rigid with spacing which lets in as much light as possible, but also seeing out through them,” explains ARM senior associate Aaron Poupard. “One of the practical considerations was that where the images lived on the facade also controls the amount of daylight that you get into the spaces. That was really important because classrooms and direct light shouldn’t ever mix.”
In addition to delivering the desired shading requirements, which contributed to the building’s sustainability credentials and 5-star Green Star rating, the fins made from 8mm XLERPLATE® steel (250 grade) steel were chosen for their aesthetic properties. “We could make it out of aluminium, but steel has a more natural quality and, particularly when it’s galvanised, it’s got a pattern on it, like a swirl, and that is actually textural,” says McDougall. “It’s quite beautiful, unlike the super refinement that aluminium brings. The actual mass and texture of it is just a beautiful, visceral thing. So when you look at it from afar, or look at it on your iPhone, you see the tattoos, the embossing, and when you look at it straight up, it’s completely abstract, and that’s another beautiful thing that texture adds.”
“One of the practical considerations was that where the images lived on the facade controls the amount of daylight that you get into the spaces”Aaron Poupard Senior Associate, ARM Architecture
With the University having selected those six artefacts from its 23 cultural collections to press into the facade, it was left to the architectural team to then determine how to generate these two- and three-dimensional objects using the chosen medium of the fins made from XLERPLATE® steel (450 grade). The architects used a number of industry-standard software packages in their process but were finding the depth element challenging, until they tried displacement mapping techniques used in gaming software to create the look of three dimensions from a two-dimensional image.
Specifically, 3D Studio Max enabled them to take the University’s chosen artefact pieces and physically imprint that in a three-dimensional way. More than 60 different spatial arrangements of the artefacts were produced for the University to choose from, which, quite apart from having to be visually balanced, had to also be positioned in a way that controlled the amount of daylight into the teaching spaces. The deeper, sculptural forms are therefore on the eastern facade – where only early, diffuse light would penetrate – while the northern facade uses large sections of less indented steel fins to limit the direct sun throughout the day. It sounds terrifically complicated, but greater challenges still lay ahead.
“The 3D model is pretty easy to get your head around, once you understand the process,” says Poupard. “But then, when you start to get into the ‘How do you actually build all that with accuracy so that every single thing lines up on each panel – so that they’re lifted into place without breaking glass?’- There’s so much precision that goes into the steel fabrication.”
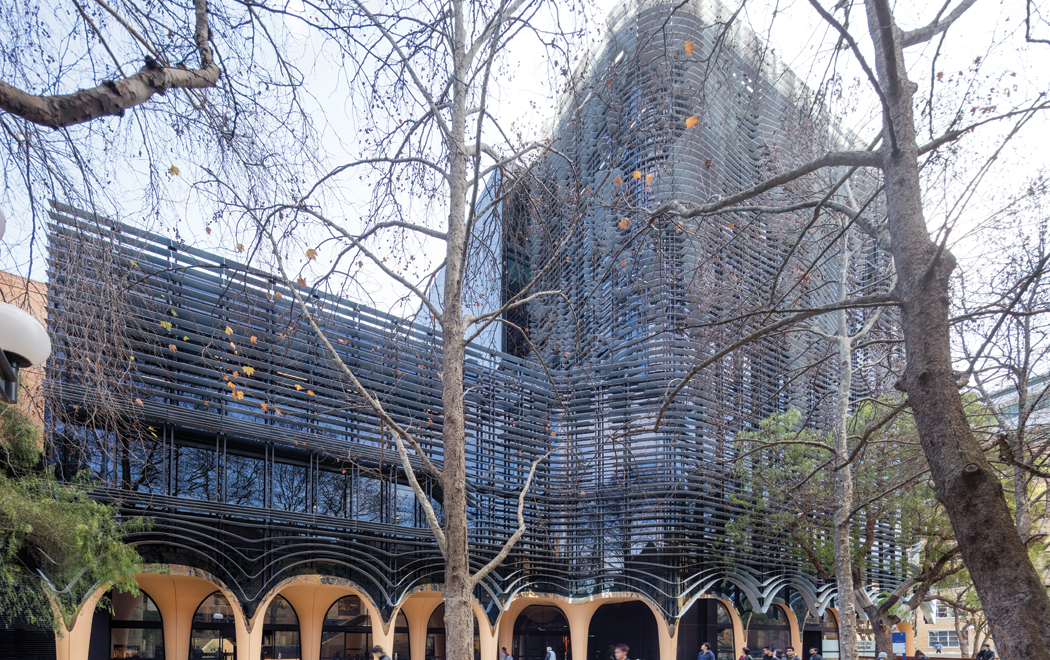
One-to-one models were made of some sections to be able to demonstrate to the client that there was sufficient visibility through the screens, but also to understand some of the other challenges of translating the design from theory to reality. For example, testing panels of fins made from XLERPLATE® steel (450 grade) for strength in wind tunnels and also to eliminate any harmonics produced in high wind, or understanding the possible distortions that galvanising causes to steel, and then being able to accommodate this modelling in the final design. “The process going from, essentially, detailed design drawings and concepts around the detailing, to working with Kane on the buildability side, to working with Fabmetal on modifying the detailing so they could make it the way they want it to manufacture it – that is absolutely crucial, that triumvirate, and it was really good in the process,” says McDougall.
For Kane project manager, Paul Christian, the facade was one of the most complex components of the overall project and generating the models was key to addressing the concerns that arose. “Prototyping eked out a number of design issues, which we then fed back to the design team to maybe adjust or tweak, but it also eked out the challenges for the contractor that we then listened to and help solve, such as welding and jigging,” says Christian.
“It’s amazing to think about a piece of steel and how it translates in the process. That facade turns the steel into an experience”
Paul Christian Project Manager, Kane
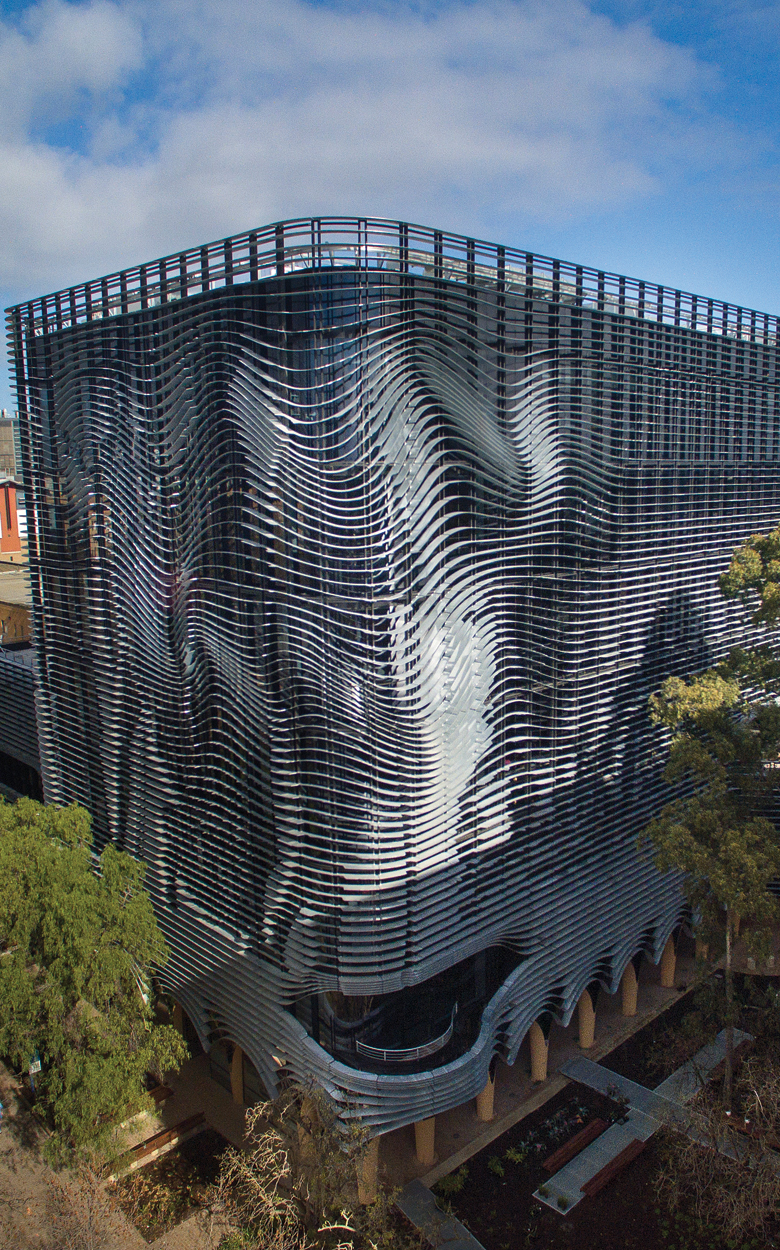
From his perspective, the project was a ‘once-in-a-lifetime opportunity’ to see steel used in such a way. “It’s amazing to think about a piece of steel and how that translates in the process,” he says. “That facade turns the steel into an experience. I don’t know of another product with which you can achieve both those aspects; where you plasma-cut something in plan to a CAD file, and then roll it in elevation, and that’s absolutely critical to the way that it behaves and then projects the images. There’s a super sense of pride associated with that building.”
Despite the challenges associated with the project, the architects have many fond and fun memories of the wider project team workshopping problems in the Fabmetal office, and then the huge benefit of being able to go straight to the shop floor, to look at the issues in-person and discuss solutions directly with the fabricators. It’s a working relationship with an embedded material information repository that has been drawn on and consolidated for the benefit of other projects, since.
“Obviously, we thought steel was fantastic, because we then used it in the Monash Chancellery [also with Kane and Fabmetal] and using a similar method, and so we learned a lot about the process,” says McDougall. “It’s a kind of cumulative knowledge that you gain. I mean, other architects ask us ‘How did you do that?’ And I’m thinking ‘It’s just easy’. And then I think, ‘Oh no, actually, we take years to get this knowledge’. But it’s not arcane, it’s not so specialised that people couldn’t also work out how to do such things. There is a bit of bravado in it, you have to say, a bit of courage. Courage on the part of the client, courage on the part of the contractors,” McDougall concludes.
Now filled with students and alive with learning, the courage of many has been rewarded with a building that has become a landmark for the University and beyond. Arts West celebrates the act and art of collecting in both self-evident and oblique ways, through the power of collective experience and via the masterful use of BlueScope’s steel.
STEEL DETAILS
A TECHNICAL DIVE INTO ARTS WEST
The teamwork and collective spirit that went into the design, fabrication and installation of the Arts West facade made from XLERPLATE® steel (450 grade) reflects one of the dictionary definitions of collaboration: ‘unity of labour’. However, it’s pretty clear that if the project group was asked to vote for a ‘player’s player’, that Fabmetal would get the gong, hands-down. “It would have been impossible to do if it weren’t for Fabmetal,” says ARM’s Poupard. “They were just fastidious, absolutely fastidious.”
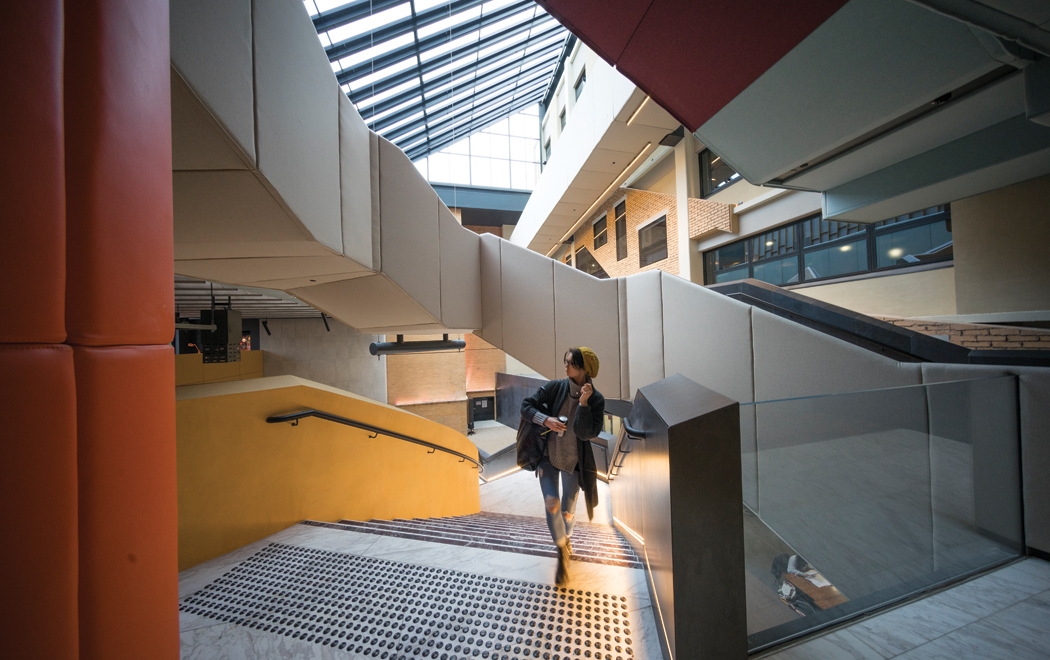
Fabmetal managing director, Gordon Heald, is matter-of-fact to the point of modesty about the experience that informs the company’s high standard of work. “I’ve been doing this a long time. Nothing’s insurmountable – the metal is metal and its first principles always apply. So really, that stuff I learned when I was a kid still applies, it’s just a bit more complicated.”
‘Just a bit more complicated’ on this project involved the fabrication of fins made 8mm XLERPLATE steel (250 grade) that are both rolled and profile-cut, which meant having to address the different tensile strengths within the various fin shapes that made up the overall pattern. The fins were fabricated as raw mild steel, and each plate had a standard dimension of 400mm and a maximum indentation of 300mm.
“As you’re rolling it, you can imagine if the material is 100mm wide, and then it changes to 300mm wide, what happens is the roll is tighter, because of the yield,” explains Heald. “If you’ve got a 300mm part, and then the tensile strength of the 300mm part is reduced to 100mm, the radius is getting tighter on the 100mm parts. So we tried to cut things either back-to-back and with little bridges in them, or leave it in a square plate with bridges in so it was 300mm wide all the way through, roll it back through and then broke out the part,” he says.
The next challenge was having to build every panel of steel fins next to its partner in the pattern, both horizontally and vertically, to ensure that they matched when finally brought together and attached to the outriggers pre-built into the inner glazed skin of the building. The panels, or modules, were six to eight metres long and 1.5 metres wide, and the facade itself was six modules by 40 modules. Assembly occurred in Fabmetal's workshop in blocks of six or eight or modules, using a special jig devised for the process, to deliver the accuracy required.
"Fabmetal came up with a jigging system," says Poupard. "It's a purpose-made linear track system with individual metal cars on bearings, with flag indicators that travelled inside the track to pre-set locations identified on the fabrication drawings.
"They would move this little flag to the exact dimension that would locate where each of the fins are meant to line up. So they'd shuffle that along the car to the right spot and then, when they bring in the fin to get welded on there, that little flag would ensure the two adjoining panels were touching, so that when they welded off each of the bits of steel, they would be in the exact location. And they did that for every single panel," Poupard says.
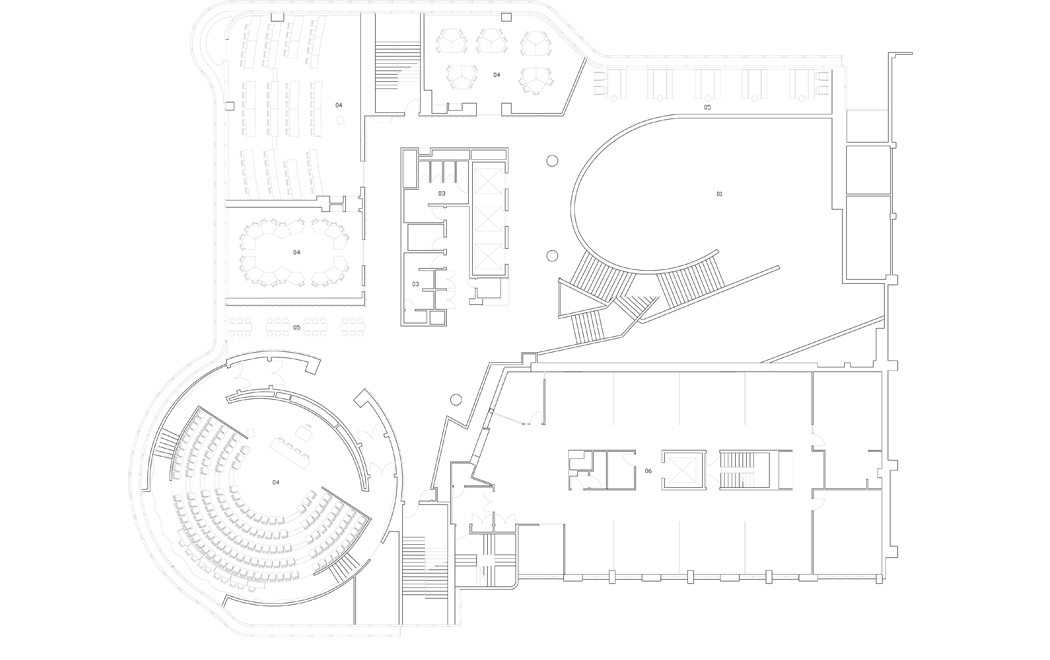
Despite these challenges, Fabmetal's Gordon Heald easily saw the advantage of steel over other materials for this project. "Steel's easier to weld than, say, aluminium; and it's more economical. And I think the practicality of putting a galvanised finish on it was a really good idea. It should be good for at least 50 years."
Complexities did not end with fabrication, and included the basic logistics of storing so many modules. Heald says the galvaniser's patience in having their yard taken over by 100-plus panels was much-valued and their overall attention to quality was ultimately acknowledged with an International Galvanising Award. In all, it was a four-month turnaround for fabrication and assembly prior to installation on-site, which Heald says still had its complications, however went relatively smoothly. He attributes this to the decades of knowledge within his own company and across the broader project team. "I've had a very stable workforce and I really appreciate my people and their abilities," he says. "I think a collaborative effort is a really important thing.
Project information
Project
Arts West, University of Melbourne
Awards
- 2017 Australian Institute of Architects National Architecture Awards COLORBOND® Award for Steel Architecture
- 2017 Australian Institute of Architects, Victorian Chapter, COLORBOND® Award for Steel Architecture
- 2017 Australian Institute of Architects, Victorian Chapter, Educational Architecture Award
- 2017 National Australian Institute of Building, Professional Excellence Awards, National Winner
- 2017 National Australian Institute of Buildings, Commercial Construction $25m to $100m
- 2017 Learning Environments Australasia Awards for Excellence, Overall Winner
- 2017 Learning Environments Australasia Awards for Excellence, An Education Initiative or a Design Solution for an Innovative Program
- 2017 Association for Learning Environments Excellence in Education Facilities
- 2017 Master Builders Australia National Commercial/Industrial Construction $50m - $100m
- 2017 Master Builders Association of Victoria Excellence in Construction of Commercial Buildings $30m - $80m
- 2017 International Design Academy Golden A Design Award - Interior Space and Exhibition Design Category
- 2017 Learning Environments Australasia Awards for Excellence, New Construction / New Individual Facility – Commendation
- 2017 Australian Interior Design Awards, Public Design, Commendation
- 2018 Intergalva Global Galvanizing Award
Location
Arts West, University of Melbourne’s Faculty of Arts building, Parkville, Melbourne, Victoria View on Google Maps
Copyright © 2022 BlueScope Steel Limited ABN 16 000 011 058. All rights reserved.
No part of this publication may be copied, reproduced or distributed without consent. BlueScope Steel Limited, to the extent permissible at law, is not liable to any person for loss or damage arising from reliance upon information contained in this publication. The articles featured in STEEL PROFILE® are sourced, written, fact-checked and curated by Indesign Media Asia Pacific with editorial contribution from BlueScope Steel Limited. Any statements or opinions attributed to a person are the views of that person alone. The decision to use any particular product or material in the projects featured in this publication was made by the team involved in each project and not BlueScope Steel Limited. While care has been taken to verify the accuracy of details in this publication, BlueScope Steel Limited assumes no responsibility or liability for any errors or omissions in the content of this publication. All information is provided with no guarantee of completeness or accuracy.
Images shown throughout have been reproduced to represent actual product colours as accurately as possible. However, we recommend checking your chosen colour against an actual sample of the product before purchasing, as varying screens and devices may affect colour tones and finishes.
Every project is different and not all products are suitable for all applications, projects and environments. Some products may perform better than others in certain applications and conditions. BlueScope generally recommends the use of COLORBOND® steel or ZINCALUME® steel for the majority of external cladding applications.
BlueScope recommends routine preventative maintenance for eaves and other "unwashed areas" of structures that may not be regularly cleaned by rainfall. To determine the most suitable material for your project, please contact your supplier or visit steelselect.com.au. For information about product maintenance, including preventative maintenance, please call BlueScope on 1800 753 658. To determine whether a warranty may be available for use of a product in your particular project, please visit bluescopesteel.com.au/warranties or call BlueScope on 1800 753 658.
COLORBOND®, XLERPLATE®, and ® colour names are registered trademarks and ™ colour names are trademarks of BlueScope Steel Limited.
Submit your project
We encourage you to share your projects for consideration in a future issue of STEEL PROFILE® magazine. We invite you to submit projects that feature a ground-breaking or an innovative use of steel. We love celebrating and writing about such projects!