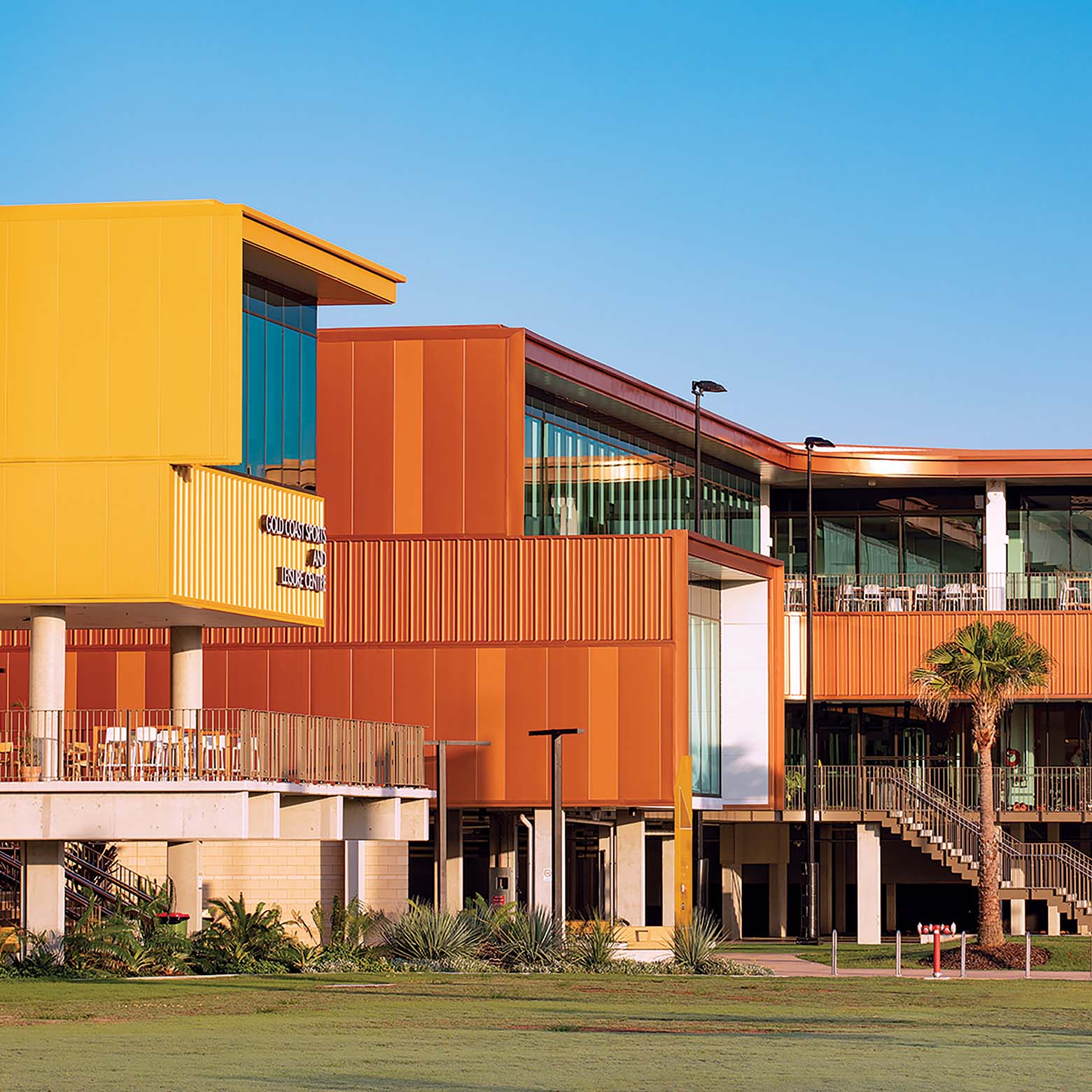
Optus Stadium
Perth’s Optus Stadium on the Burswood Peninsula harnesses the strength of steel to take sports and entertainment experiences to the next level.
Words: Lucy Salt.
Photography: Peter Bennetts
Project Summary
Optus Stadium’s three key architects - HASSELL, COX Architecture and HKS Architects - collaborated to fulfil the design vision for a distinctly Western Australian, world-class sports and entertainment facility - underpinned by BlueScope steel.
The Stadium incorporates approximately 4500 tonnes of BlueScope welded Beams and columns, 3000 tonnes of XLERPLATE® structural steel, and 1300 tonnes of DECKFORM® steel supplied by Lysaght and Fielders.
Crown Jewel
Underpinned by a voluminous yet visually lightweight structure made from approximately 7500 tonnes of BlueScope steel, Perth’s Optus Stadium has rapidly fulfilled the design vision for a distinctly Western Australian, world-class sports and entertainment facility.
Since opening in late 2017, Optus stadium has garnered a swag of awards, key amongst which was the 2018 Australian Institute of Architects National COLORBOND® Award for Steel Architecture and the National Award for Public Architecture – the former described by the jury as “a compelling and worthy contribution to Australia’s steel architecture tradition.”
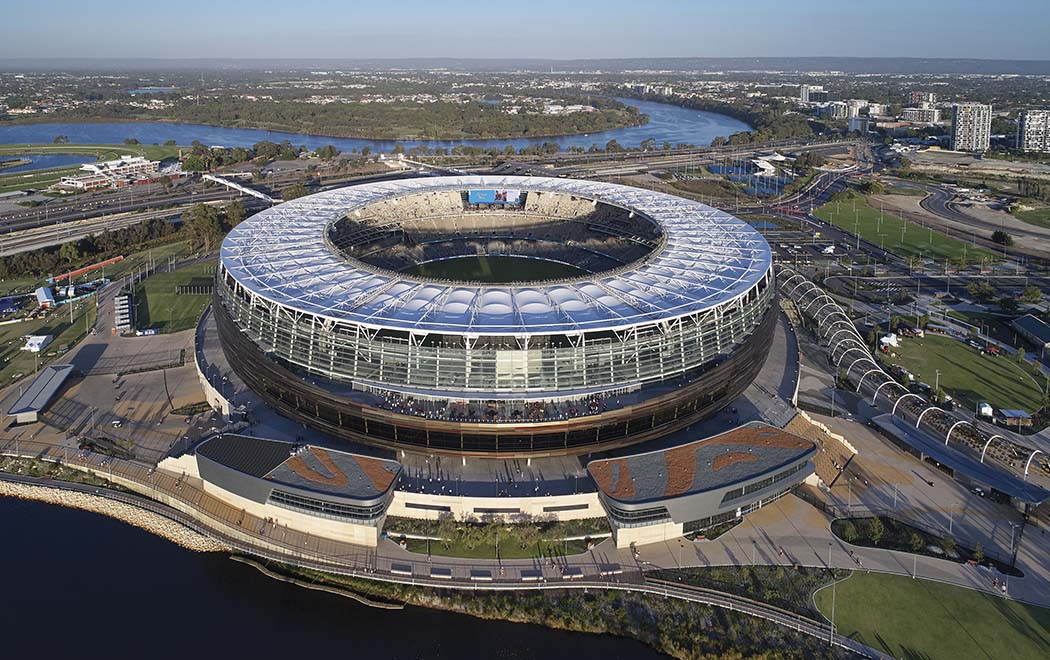
The brief called for a world-class, fans-first stadium fully embedded within an active public realm - an ambition that would become the reigning mantra for the competition-winning design team lead by Hassell in association with COX Architecture and HKS Architects.
For their part, Hassell, COX and HKS all immediately recognised the project’s potential as a game-changer for the Western Australia capital. Here was an opportunity to take a long-neglected, relatively isolated site and restore it for the public’s enjoyment.
“We all shared a vision for the whole-precinct approach and how the site could be regenerated, and returned to the people,” says Matthew Batchelor, director at COX Perth. The steel superstructure allowed the metal wall cladding to be highly discontinuous and light, to make the stadium as transparent and connected to the landscape wherever possible. “It looks quite solid from the outside, but the discontinuities - along with the extensive glazing - mean that as you’re walking through it you’re connecting back to the landscape,” Batchelor says.
“We don’t get sites as good as that very often,” says Paul Hyett, the London-based director of sports at HKS. “It’s the most beautiful setting on a bow in the river and visible from parts of the city.”
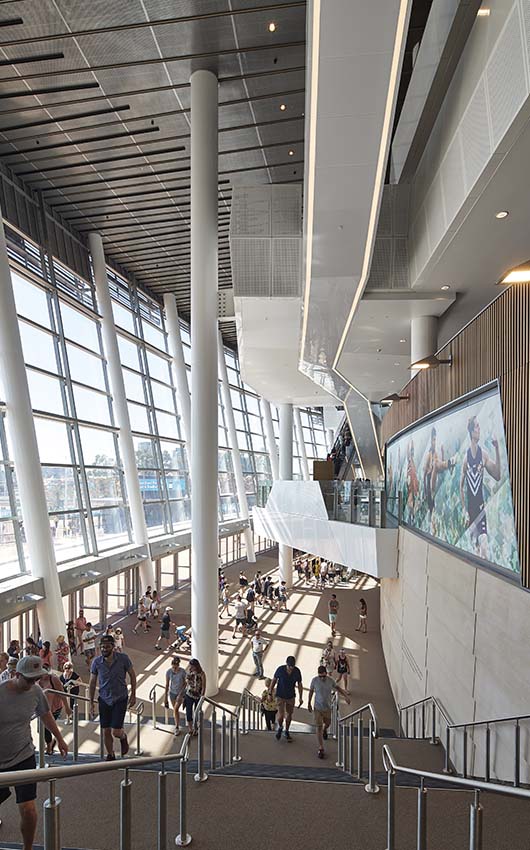
In many ways, steel is the ultimate hero of the project. “The steelwork gives the building its aesthetic appeal and character,” says Hyett. “Steel is the most wonderful material for architects, it combines incredible strength within relatively small sections and it’s also something which you can easily form and shape.
“The roof of that building, with the cantilevered steel trusses tied at the back and the way in which that roof is working, structurally, is expressed in its appearance. The combination of the steel and the fabric has given the most incredibly light feel to it,” he says.
BlueScope supplied all of the primary steelwork – 4500 tonnes of welded beams and columns and 3000 tonnes of XLERPLATE® steel - via WA distributors, InfraBuild. Another 1350 tonnes of steel decking was supplied by Fielders and LYSAGHT®.
“Steel is the most wonderful material for architects, it combines incredible strength with relatively small sections and it’s also something which you can easily form and shape.”Paul Hyett Director of Sport, HKS (architect)
The architects say steel was integral to the construction program of the five-level superstructure and the ambitious design performance requirements of the ‘floating’ roof structure. Featuring more than 15,000 fabricated steel components, the works included the installation of 50 major structural trusses that support the tensile fabric roof canopy that shelters up to 85 percent of spectators.
The architectural and structural geometry of the roof was also developed to address an ambitious program requiring steel pre-fabrication, as well as transportation and erection challenges. The cleverly designed pin-joint system with tolerances to absorb differential movements across the structure below, and to allow fine-tuning to ensure alignment of the leading edge, results in a stunning and efficient halo roof solution.
For Dean, it was important that materials were expressed honestly - with all primary steel structure coloured white, and a grey secondary steel structure - to create a decipherable building lexicon.
“As a muse, steel’s malleable, adaptable form has been interrogated extensively, from its piled structure to help overcome difficult ground conditions, large spans in the roof trusses for obstruction-free views, feature columns, beams and seating bowl rakers to the dramatic geometry of the pedestrian arbour,” Dean says.
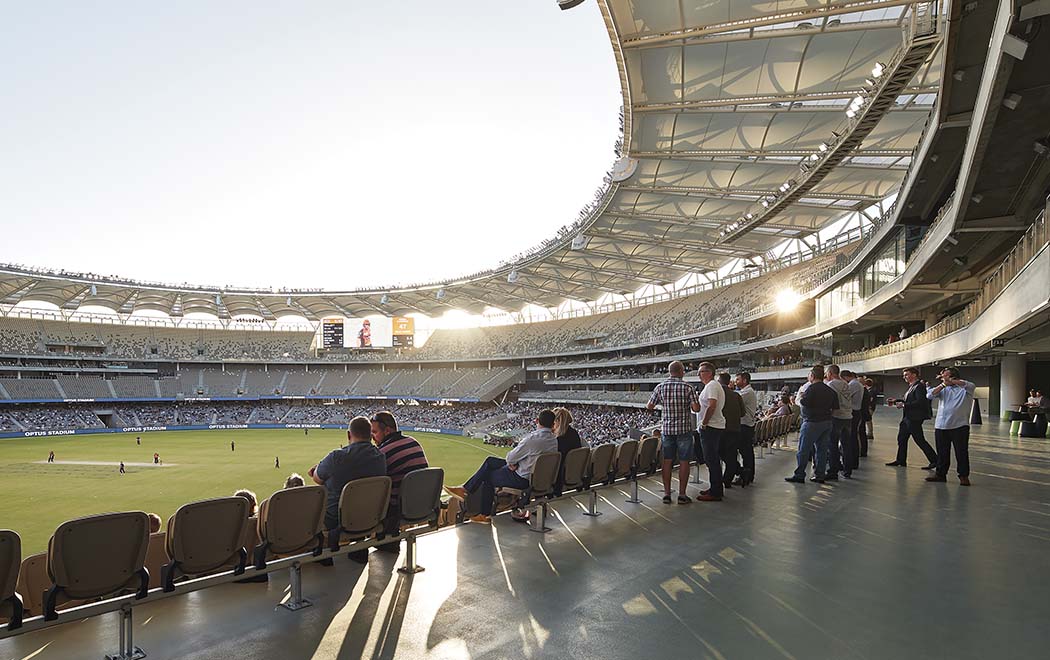
“The generous spans in the trusses allowed us to get large elements, such as function rooms, underneath the seating bowl without transferring any structural columns out,” he continues. In addition, the steel columns facilitated consolidated services to minimise costs and keep fans closer to the field-of-play, rather than lifting them further away from the action.
“There was a lot of engineering and collaborative work with Arup and Multiplex to refine the design of the steel frame members, and particularly the truss,” says Batchelor, who describes the finely detailed pivot-knuckle joint designed into the truss base which allowed the trusses to be placed relatively simply – mitigating the need to work at height as much as possible.
The steel trusses themselves were prefabricated by Civmec in nearby Hendersen, then transported to site where all the cladding elements, including the fabric roof modules, were added and craned up as a single element. “At the height of construction we had nine trusses down on the ground being assembled while one was being lifted into place, it was a really interesting construction program,” says Batchelor.
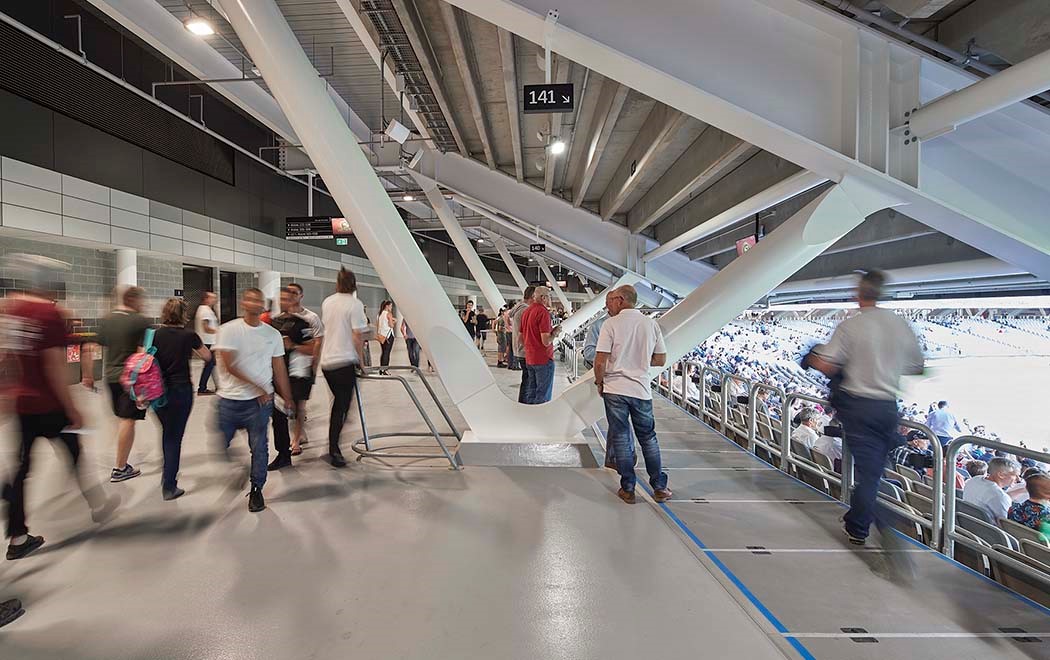
The construction and erection methodology was a key innovation, agrees Dean. With construction proceeding with basement works at one end and roof works at the other, the cantilevered, triangular trusses were designed to free-stand after three bays were erected. “The roof had to be free-standing because it was never complete until the last bay went together,” says Dean.
The way the design was transferred into fabrication is, for Dean, an under-recognised aspect to be celebrated. “The fabricators went through hell and high water over an 18-month period to deliver the project on time. It’s no easy feat, particularly with a fast-tracked project, and a constantly evolving design.”
Of his experience in Perth, Hyett says “On this occasion we were able to fuse the ability and the commitment of Australians to good architecture with the Australian love of sport. It was a wonderful marriage and I was very happy to be there in the middle.”
What matters about the stadium for Dean is that the architects have created a memorable Western Australian emblem, and in turn have set a new benchmark for what people in WA expect from these kinds of projects: “Usually you say there have been compromises, but this project got better and richer because of peoples’ commitments. It was a career-defining moment for everyone involved.
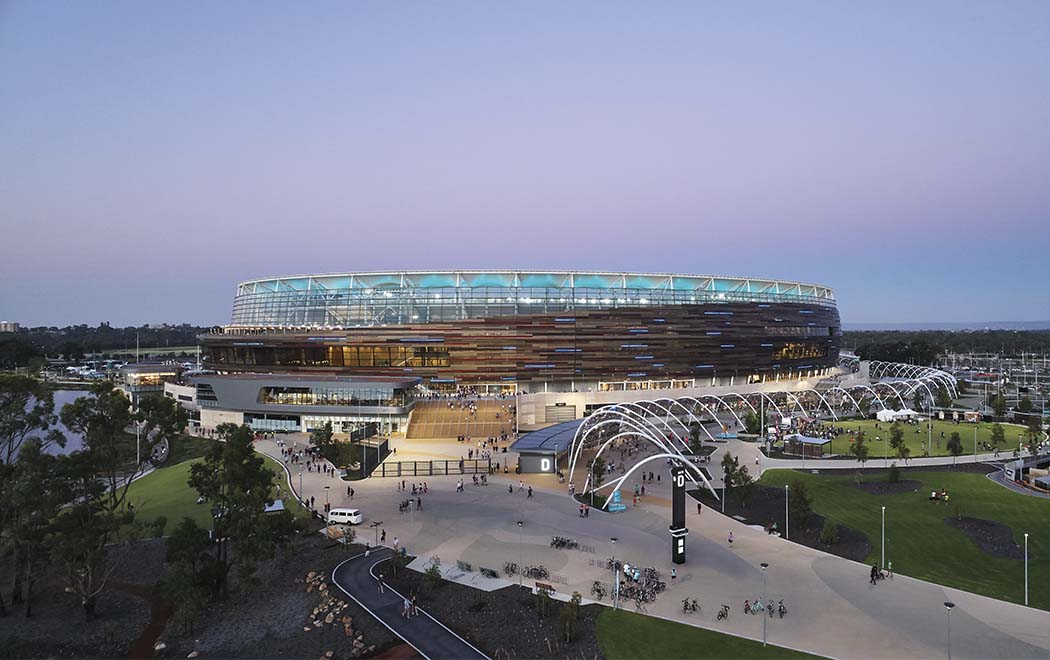
Panel Says
This impressive sports and events facility in Perth has an arresting appearance which makes the most of its magnificent waterfront location. Sited on a peninsula opposite the CBD, the stadium is accessed from all sides, and delivers on its promise of a ‘fans- first’ experience, both inside and outside the arena.
BlueScope supplied all of the primary steelwork - 4500 tonnes of welded beams and columns and 3000 tonnes of XLERPLATE® steel - that is pivotal to the project’s success. The design reveals exposed columns, beams and pin-joints that express a monumental skeleton supporting vast sections of high-level glazing. This strong and visible framework enables the peripheral circulation spaces to be naturally lit, and to capture views outwards in all directions. Inside the main arena, a delicate, steel-framed, lightweight roof canopy provides protection from the elements, further enhancing the spectator experience at this world-class facility.
Project information
Architects
Hassell
COX Architecture
HKS Architects
Project
Optus Stadium, Perth Western Australia
Awards
- 2018 Australian Institute of Architects National COLORBOND® Award for Steel Architecture and National Award for Public Architecture
- 2018 Australian Institute of Architects Western Australia Chapter Awards – COLORBOND® Award for Steel Architecture, George Temple Poole Award, Jeffrey Howlett award for Public Architecture, Wallace Greenham award for Sustainable Architecture
- 2018 Australian Institute of Landscape Architects Western Australia Chapter Awards – WA Medal for Best Project, Play Spaces Award of Excellence, Urban Design Award of Excellence
Location
Optus Stadium, 333 Victoria Park Drive, Burswood WA 6100 View on Google Maps
Copyright © 2019 BlueScope Steel Limited ABN 16 000 011 058. All rights reserved.
No part of this publication may be copied, reproduced or distributed without consent. BlueScope Steel Limited, to the extent permissible at law, is not liable to any person for loss or damage arising from reliance upon information contained in this publication. The articles featured in this edition of STEEL PROFILE® are sourced, written, fact-checked and curated by the authors with editorial contribution from BlueScope Steel Limited. Any statements or opinions attributed to a person are the views of that person alone and do not necessarily reflect those of BlueScope Steel. The decision to use any particular product or material in the projects featured in this publication was made by the team involved in each project and not BlueScope Steel Limited. While care has been taken to verify the accuracy of details in this publication, BlueScope Steel Limited assumes no responsibility or liability for any errors or omissions in the content of this publication. All information is provided with no guarantee of completeness or accuracy.
Images shown throughout have been reproduced to represent actual product colours as accurately as possible. However, we recommend checking your chosen colour against an actual sample of the product before purchasing, as varying screens and devices may affect colour tones and finishes.
Every project is different and not all products are suitable for all applications, projects and environments. You should confirm the suitability of particular products for your project by contacting the supplier directly and by obtaining information and advice specific to your circumstances.
To determine whether a BlueScope warranty may be available for use of a product in your particular project, please visit bluescopesteel.com.au/warranties.
BlueScope, XLERPLATE®, LYSAGHT®, Fielders®, and DECKFORM® are registered trademarks of BlueScope Steel Limited.
Submit your project
We encourage you to share your projects for consideration in a future issue of STEEL PROFILE® magazine. We invite you to submit projects that feature a ground-breaking or an innovative use of steel. We love celebrating and writing about such projects!