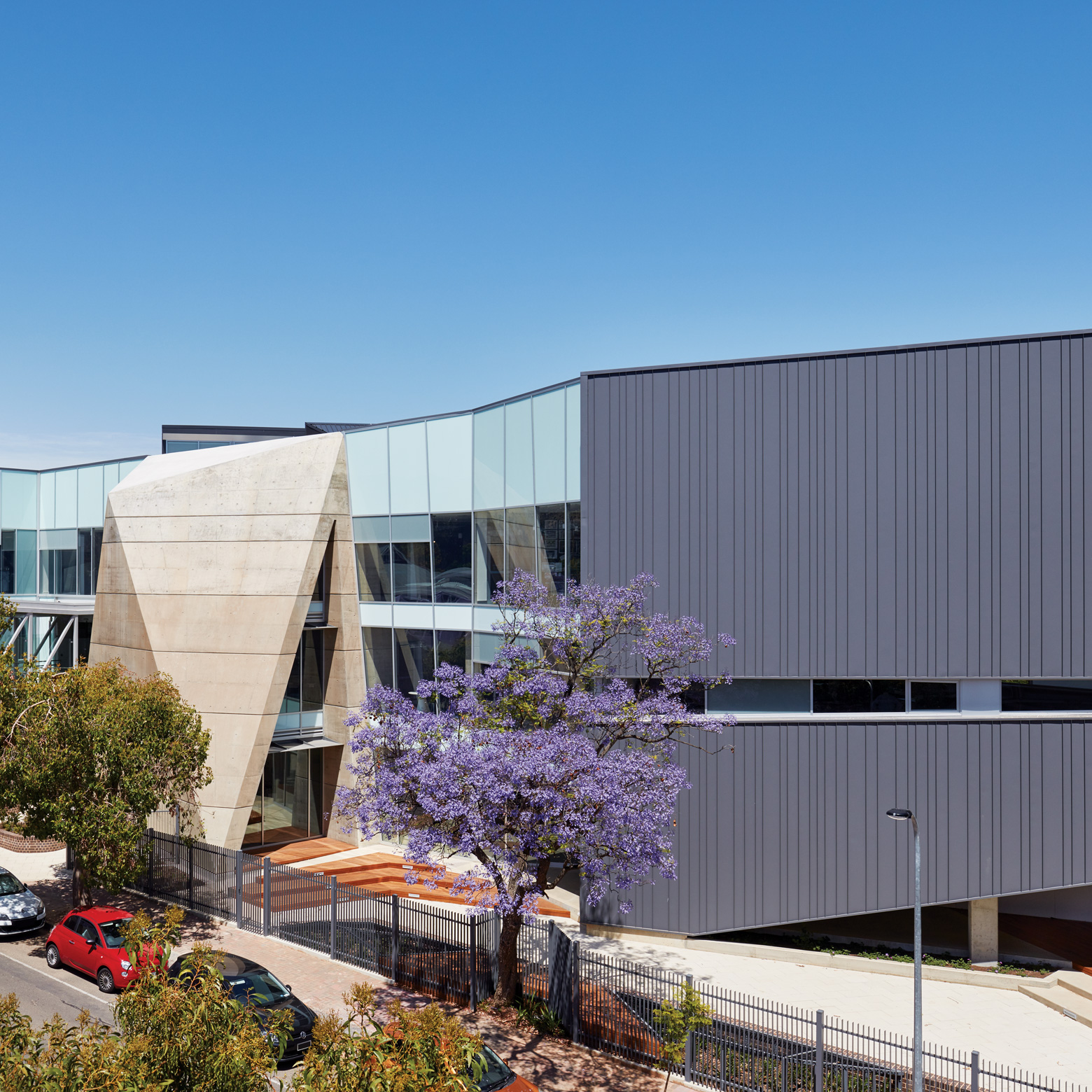
Warren Integrated Studies Hub
The design for a new wing at Warren Integrated Studies Hub draws on biophilic principles to craft stunning curves and an eye-catching roofing profile using LYSAGHT LONGLINE®.
Words: Micky Pinkerton.
Photography: Jarryd Sinclair
Videography: The Local Production
Project Summary
The design for a new wing at Warren Integrated Studies Hub draws on biophilic principles to craft stunning curves and an eye-catching roofing profile using LYSAGHT LONGLINE®.
Natural Wonder
Informed by biophilic design, this eye-catching roof made from COLORBOND® steel in the colour Surfmist® on the new wing of a Sydney school swoops and swirls, inspiring students and providing the perfect project to showcase an adaptable LYSAGHT LONGLINE® roofing profile.

There’s a reason why most buildings are rectangular – it’s an easier shape to build. Throw in a curve and you’re upping the ante on the abilities of all involved – and asking a lot more from your materials. But with increasing trends supporting the benefits of educational environments with designs drawn from the natural world, Mayoh Architects was undaunted. The design draws on the outstanding technical properties of a steel roofing product that marries the renowned proven qualities of COLORBOND® steel with a specialised LYSAGHT LONGLINE® profile that tapers to achieve the impressive organic arc of the building’s roof.
That tenacity and daring have since been rewarded with the 2023 Australian Institute of Architects NSW Chapter COLORBOND® Award for Steel Architecture, and the rounded roof in Surfmist® has become symbolic of the school’s identity, proudly demonstrating innovation in construction and aptly reflecting the scientific learning happening beneath it.
Mayoh associate, Jonathan Henley, explains that the LYSAGHT LONGLINE® 305 tapered profile was the preferred product to meet the objectives of the brief. In fact, this design decision also led to a reduction in waste due to the form of the panels. “It was cost-effective, required little maintenance and resulted in less construction waste from a sustainability perspective, as well as meeting the aesthetic aspirations of the design,” explains Henley.
“We looked into a few different options that would help with the curves,” continues Henley. “What we really didn’t want was a series of straight roof sheets with overlapping flashings in triangular form – that could have been problematic for water leaking and it’s a real maintenance issue. So we reached out to Lysaght and we said, “This is our design, what can we do?”
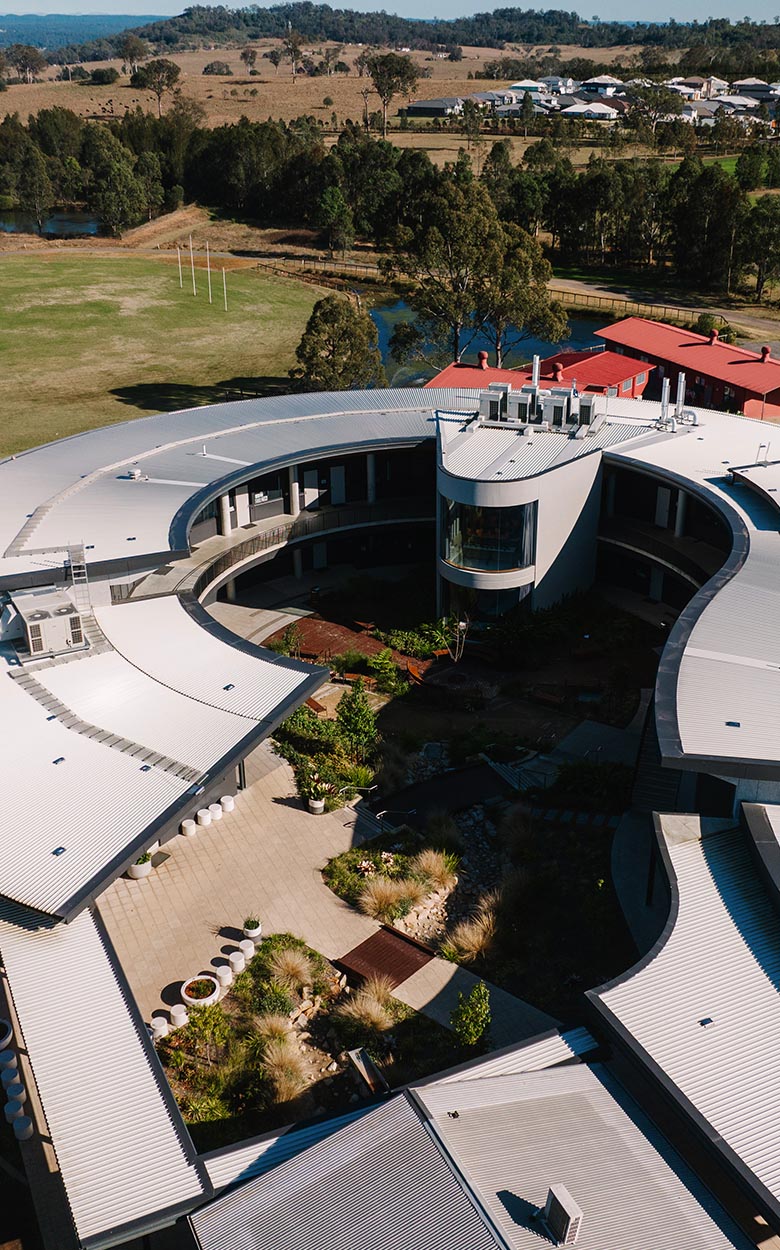
LYSAGHT LONGLINE® 305 was identified as a product solution which would allow the custom rolling of tapered sheets to match the curve of the roof shape. In short, a standard 305-millimetre-width cover is concertinaed at one end to a narrow dimension of 155 millimetres, with ribs radiating from a central point, creating a beautiful fan effect. The same concealed fixings as the standard LYSAGHT LONGLINE® 305 product are used to clip sheets together, meaning that there are no penetrations.
The architects, meanwhile, observed significantly reduced material waste in general, thanks to the design decisions that the material was able to facilitate. “The steel roof was a much more sensible option than other materials, which could have had a lot of wastage in that curve form, whereas the roofing made from COLORBOND® steel in tapered LYSAGHT LONGLINE® profile, and even the structural steel supporting it, was much more flexible,” says Henley.
Sustainability was a key client focus, not just in design and construction but also for ongoing operation and maintenance. The building features abundant natural light, natural ventilation (on all but the hottest and coldest days of the year), large overhangs for sun shading and quality insulation, while water is harvested from the roof into the courtyard’s dry riverbed plantings.
“Design that mimics nature makes people feel more comfortable. [The natural environment] is the place we feel most tranquil.”Jonathan Henley Mayoh Architects
The selection of the Surfmist® colour also contributes to better thermal performance, being one of eleven shades in the COLORBOND® steel core colour range which feature low Solar Absorptance (SA) values of less than or equal to 0.45 and meet Section J energy efficiency provisions to mitigate against the effects of Urban Heat Islands.
“At all of our meetings that we had with the school, the maintenance team was there as well,” says Henley. “We really wanted all of the materials, and especially the roof, to be low-maintenance or essentially maintenance-free.
“Something that we generally do in all of our school designs is plan for the future. So that flexibility – being able to have a portal frame that allows all the internal walls to be non-structural so the school can change that in 10 or 15 years, and maintain the life of the building through changing uses – that was very useful.”
For indicative lifespan, the school had the adjacent Arts building with 20-year-old roofing made from COLORBOND® steel, which Mayoh Architects assessed for refurbishment as part of the same engagement. The old roof sheets made from COLORBOND® steel were still in excellent condition and only a small portion had to be replaced at the new junction between the two buildings.
Resolving the complex design, however, was not without its challenges. The calculations required to determine the radius of each separate LYSAGHT LONGLINE® 305 roof sheet made from COLORBOND® steel were significant (see Steel Details), a hidden guttering system had to be devised and a flashing solution arrived at for the tight inside curve of the roof’s upper edge.
Due to the large overhang, having gutters on the exterior of the building would have required downpipes to penetrate the continuous vertical louvres around the perimeter – an unsightly response which would have impacted on the carefully designed blades that vary in spacing and depth to suit the solar orientation inherent in a radial external facade, and meet Section J compliance. A hidden gutter detail was developed to solve this, allowing the downpipes to run along the exterior walls. As these were spaced at the vertex of each faceted section of wall, these corners were hidden, accentuating the building’s sense of curvature. A coordinated effort between Mayoh Architects, builder Reitsma Constructions and roofing contractor BRC made this possible.
A further challenge was the roof span, which was slightly longer than the maximum length of sheet possible at the radiuses required. “So we had a maximum spacing at gutter, and then it splayed in to a narrower spacing on the inside of the curve,” explains Henley. “But at that point, we were still short of the width of the building. We essentially have about 700 millimetres of flashing to the curved steel PFC beam on the inside edge, and that worked out really well.”
This solution is visible on the inside curve at the high point of the roof and, again, was arrived at through on-the-ground brainstorming with the builder and roofing contractor.
“Something that we generally do in all of our school designs is plan for the future.”
Jonathan Henley Mayoh Architects
Reistma Constructions manager, Matthew van Bentum, says collaboration is critical for these more challenging designs: “There’s lots of workshopping that has to be done, because it’s not just a square or rectangular building, everything is worked off radius points. There’s lots of set-out to work through from a site perspective – a lot of coordination needs to happen with the roofer and the architect around some of that additional detailing that’s required. But to be honest, there’s not really any other option on a curved building like this.” Van
Bentum agrees that the tapered LYSAGHT LONGLINE® 305 profile is an ideal product for such a roof design. “Because you don’t want to have a scenario where you’re trying to do cut sheets and flashings to try and draw in profiles all the way around the building, you need to be able to have the sheet interlock all the way around, to have a seamless transition around the length of the building,” he says. “The most effective way you can achieve that is through tapering of the roof sheets.”
The spirit of collaboration that underpinned the building’s construction is now evident in the work of the students within it. Given that more traditional classrooms were formerly prevalent across the campus, there was a desire from the school and the architects to deliver flexible learning environments that support teamwork, creativity and critical thinking. These spaces have a strong visual and physical connection to the central courtyard with its soft, permeable edges. It is this courtyard which Henley says has become his favourite part of the project for the different ways that the students use it: racing robots made in the new maker space being run along its paths; the rain chain in the dry riverbed being used for science experiments and art projects; student-generated signage about the sustainability of the building dotted around the space.
“Being able to see all the different disciplines having those connections from one central area feels like a real precinct for learning STEAM projects, rather than a series of separate disciplines,” Henley says.

Henley is convinced of the merits of biophilic design: “There’s a lot of research indicating students who have natural airflow or natural light and connection to nature are calmer – they have better learning outcomes, and it’s just a more pleasant space to be in, so they can focus.
“Design that mimics nature makes people feel more comfortable. We evolved in the natural environment and that’s the place we feel most tranquil, so I think the way to go is to mimic that as much as we can with our built environment.”
No doubt the generations of Australians who started school in boxy, sweaty demountables will agree. With tapered roofing products now making curved constructions such as Warren Integrated Studies Hub easier and more affordable, it looks like we’ll be seeing more organic shapes at the school gate in future.
STEEL DETAILS - A TECHNICAL DIVE INTO WARREN INTEGRATED STUDIES HUB
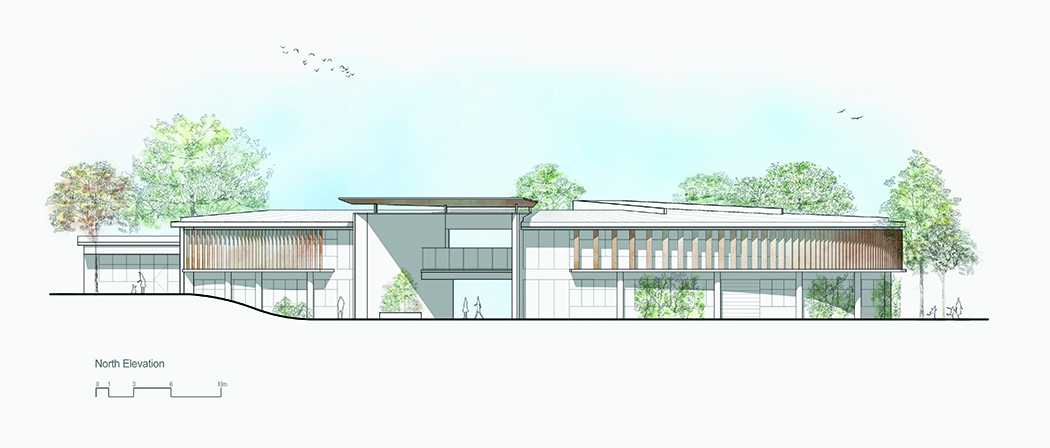
LYSAGHT LONGLINE® 305’s tapering capabilities allows fanned and rounded-plan roof shapes to be clad with ribs radiating from a central point. In short, it is a game-changer for achieving the natural forms associated with biophilic design. However, its use requires some ‘curly’ calculations and Mayoh Architects called on the experience of two individuals in particular to help understand what was involved: Will Pereyra at Lysaght and Blake Allen, director at BRC Roofing and Cladding.
Pereyra started his career as a structural and architectural draughtsperson for a number of engineering firms and says this background has been hugely beneficial in his role as a business development manager with Fielders and Lysaght. With an inherent knowledge of the LYSAGHT LONGLINE® 305 product, even he concedes that the Warren Integrated Studies Hub required some intricate pre-planning.
“The project had its complexities in the fact that it snaked in the other direction and you were dealing with different radiuses, and also the falls and levels are in different directions,” says Pereyra. “It took eight hours’ worth of calculations just working out the tapers, the quantities and what percentage of sizing was required for one section.”
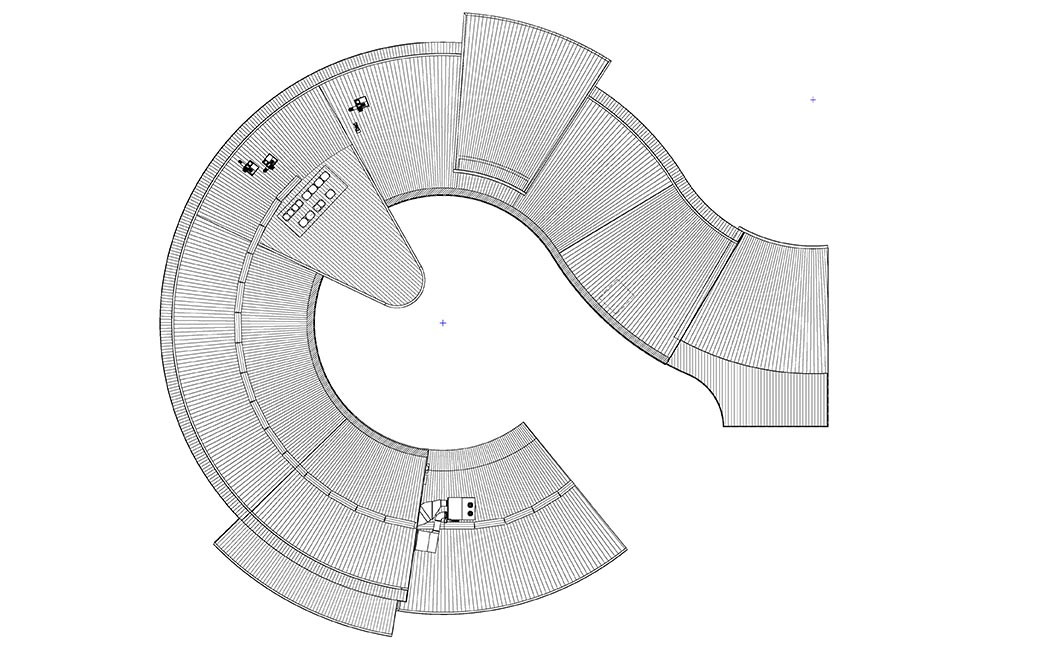
Tapering introduces much finer tolerances (both on-site and on the machines rollforming the sheets) where just a couple of millimetres can be critical. So while plans and 3D models provided crucial guidance and intent, the individual segments were ultimately measured from the physical steel structure for greater accuracy.
“Lysaght LONGLINE® is not like our other profiles such as CUSTOM ORB®, where you can actually stand on it and spread it out, and sort of massage it into place,” Pereyra says. “We really need to work with what’s on-site with Lysaght LONGLINE®, so that’s when I got a bit more involved with the builder and the installer and explained how the curve could start pulling in towards itself, if you don’t keep checking these things.”
For Allen, who had worked with the product before but not on this scale, that meant “recalibrating regularly on every stage of it, on every order. That was one of the challenges, getting the taper exactly right,” he adds.
“For each few sheets we laid, we would have a datum point and that might give us a reading that we needed to step back this much, and so we’d need to increase the next 30 sheets by maybe one millimetre here or there”.
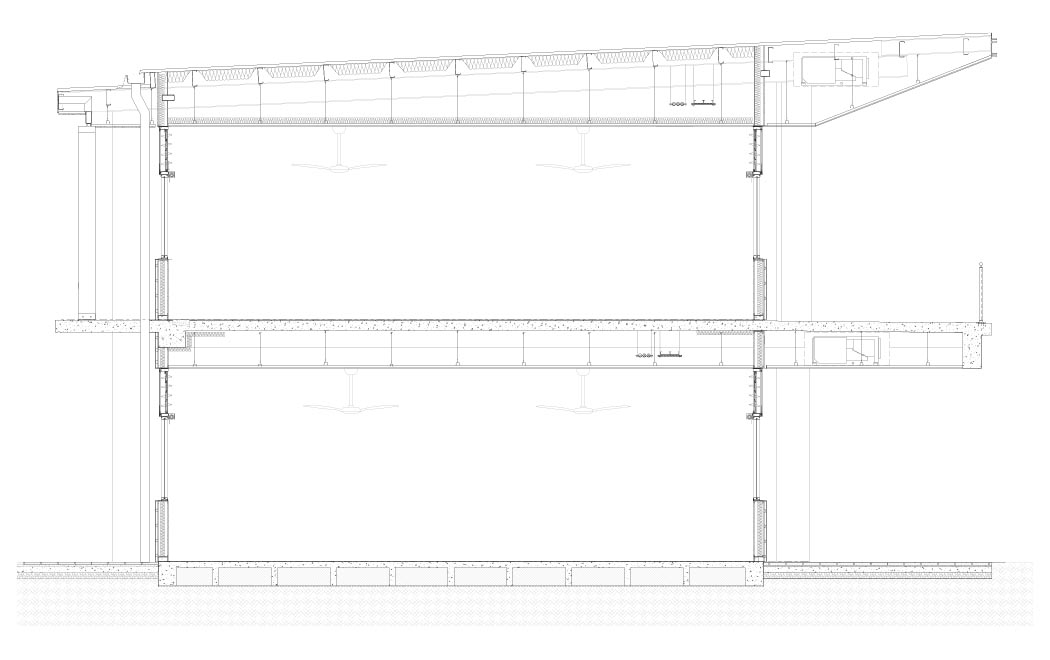
To assist with this process, Allen and Pereyra developed a flat sheet template which showed the radius of the sheet direction and allowed them to double check that they were staying true, before confirming the size and taper of the panel as marked-off on-site. Sheets were then produced back at the Lysaght factory and delivered in stages. Allen says such projects are challenging in every respect but add vital experience – for example, even setting up safety rail and safety mesh on a curved edge is a different process.
“I like these projects because, on paper, we don’t know exactly how we’re going to do them but we pull together a team around us,” he says. “We had our external stakeholders such as Will at Lysaght, and we were going to pull together and roll our sleeves up and have a go. So that aspect is a driver, because it feeds our passion and purpose.”
TO LEARN MORE ABOUT THE PROJECT, PLEASE WATCH THE VIDEO BELOW.
Project information
Architect
Mayoh Architects
Project
Warren Integrated Studies Hub
Awards
- 2023 Australian Institute of Architects NSW Chapter – COLORBOND® Award for Steel Architecture
- Learning Environments Australasia, NSW Chapter – New Facility (Winner 2023)
- Learning Environments Australasia - New Building or Facility – Large (Commendation 2023)
- Learning Environments Australasia – New Construction Over $8m (Commendation 2022)
- Urban Development Institute Australia (UDIA) – Social & Community Infrastructure (Finalist 2022)
Location
605 Cobbitty Road Cobbitty, NSW 2570 View on Google Maps
Copyright© 2023 BlueScope Steel Limited ABN 16 000 011 058. All rights reserved.
No part of this publication may be copied, reproduced or distributed without consent. BlueScope Steel Limited, to the extent permissible at law, is not liable to any person for loss or damage arising from reliance upon information contained in this publication. The articles featured in STEEL PROFILE® are sourced, written, fact-checked and curated by Indesign Publishing Pty Ltd ABN 96 101 789 262 T/A Indesign Media Asia Pacific with editorial contribution from BlueScope Steel Limited. Any statements or opinions attributed to a person are the views of that person alone. The decision to use any particular product or material in the projects featured in this publication was made by the team involved in each project and not BlueScope Steel Limited. While care has been taken to verify the accuracy of details in this publication, BlueScope Steel Limited assumes no responsibility or liability for any errors or omissions in the content of this publication. All information is provided with no guarantee of completeness or accuracy.
Images shown have been reproduced to represent actual product colours as accurately as possible. However, we recommend checking your chosen colour against an actual sample of the product before purchasing, as varying screens and devices may affect colour tones and finishes.
Every project is different and not all products are suitable for all applications, projects and environments. Some products may perform better than others in certain applications and conditions. BlueScope generally recommends the use of COLORBOND® steel or ZINCALUME® steel for the majority of external cladding applications.
BlueScope recommends routine preventative maintenance for eaves and other “unwashed areas” of structures that may not be regularly cleaned by rainfall. To determine the most suitable material for your project, please contact your supplier or see steelselect.com. au. For information about product maintenance, including preventative maintenance, please call BlueScope on 1800 064 384. To determine whether a warranty may be available for use of a BlueScope product in your particular project, please visit bluescopesteel.com.au/warranties or call BlueScope on 1800 064 384.
COLORBOND®, LYSAGHT®, CUSTOM ORB®, and LONGLINE®, and ® colour names are registered trademarks of BlueScope Steel Limited.
Submit your project
We encourage you to share your projects for consideration in a future issue of STEEL PROFILE® magazine. We invite you to submit projects that feature a ground-breaking or an innovative use of steel. We love celebrating and writing about such projects!